Travailler pour les fabricants de dispositifs médicaux : un choix qui ne s’improvise pas
La PME franc-comtoise DDLG (Décolletage de la Garenne) a développé une expertise de pointe dans la réalisation de DMI de classe II et III en inox et en titane. Fort de son succès, son président Yannick Robichon, qui a repris l’entreprise en 2013, passe la vitesse supérieure et investit pour faire du médical son activité principale. Il est convaincu que ce marché exigeant ne se contente pas de la demi-mesure.
Le 30 mars dernier, alors que la crise du COVID-19 bat son plein, DDLG est contacté en urgence pour une commande de 8000 pièces de respirateurs à livrer avant la fin du mois. La demande émane d’un de ses clients suisses, qui connaît déjà la rigueur avec laquelle l’entreprise applique les exigences réglementaires du secteur médical : qualification de tous les process d’usinage mis en œuvre et du personnel utilisateur, usage de machines dédiées, conservation et scannérisation de toutes les gammes de contrôle… DDLG est bien sûr certifiée ISO 13485:2016. Le président de l’entreprise Yannick Robichon relève le défi dès le lendemain, soutenu par une équipe très enthousiasmée à l’idée d’apporter sa contribution aux patients les plus lourdement contaminés.
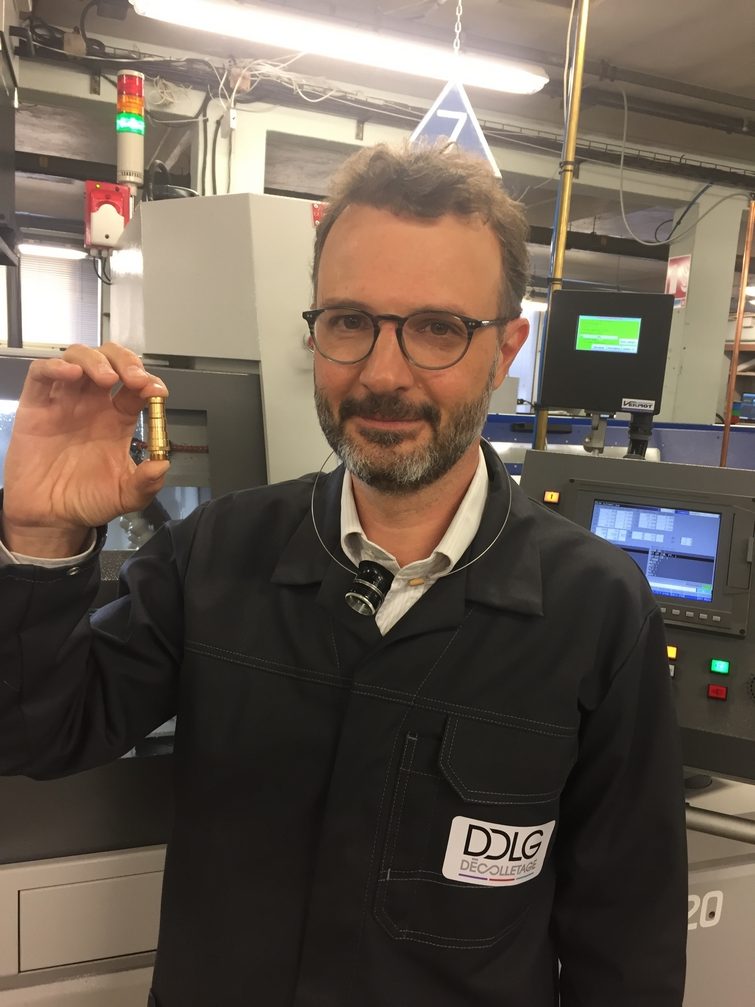
Yannick Robichon et son équipe ont réalisé cette pièce de connectique en laiton pour respirateur, dans le cadre de la lutte contre le COVID-19 (source DDLG).
Il se trouve que DDLG a déjà développé par le passé un process pour produire des composants similaires, même si l’application était différente. Il s’agit de connecteurs très fragiles en laiton qui ne doivent pas subir le moindre choc ni la moindre oxydation, et dont les tolérances dimensionnelles sont extrêmement serrées (±0,01 mm pour bon nombre de cotes). Chaque pièce doit faire l’objet d’une cinquantaine de points de contrôle. A la complexité dimensionnelle s’ajoute la nécessité d’un excellent état de surface, permettant au client de soumettre ultérieurement la pièce à un traitement amagnétique.
Les connecteurs ont été réalisés par décolletage sur un tour 6 axes de marque CITIZEN avant de subir une opération de tribofinition fine. Comme toutes les pièces médicales fabriquées par DDLG, ils ont ensuite été soumis à un contrôle à 100 % au moyen d’un microscope d’inspection visuelle 3D Mantis. Les pièces sont ainsi grossies de 3 à 4 fois, ce qui garantit un contrôle minutieux et précis.
« Nous avons atteint l’objectif que nous nous étions fixé » indique Yannick Robichon, qui est parvenu à livrer les 8000 connecteurs avec une semaine d’avance, dans le souci d’aider son client à accélérer la production des respirateurs.
Une solide expertise en DMI de classes II et III
Il ajoute : « Les contraintes de fabrication étaient assez similaires à celles auxquelles nous sommes confrontés quand nous produisons des chambres implantables, l’un de nos domaines d’expertise. Si les implants présentent des aspérités, cela peut provoquer une accroche plaquettaire lors du reflux sanguin qui a cours durant la phase initiale d’aspiration servant à vérifier que le cathéter est toujours bien relié à la veine. Il en résulte un risque d’infection. L’état de surface doit donc être excellent. Ici aussi nous avons recours à la tribofinition. » DDLG livre ces chambres implantables soudées, polies et finies. Il suffit à son client de les décontaminer et d’y apposer le septum.
La certification ISO 13485 : un MUST pour les sous-traitants
DDLG a confié il y a quelques mois à deux étudiants de l’ISIFC la réalisation d’une étude de marché auprès de 30 fabricants de dispositifs médicaux implantés autour de Besançon. L’un des objectifs était de connaître l’importance qu’ils accordaient à la certification ISO 13485 de leurs sous-traitants. Si la part de fournisseurs certifiés est aujourd’hui de 25 % en moyenne chez ces fabricants, l’étude a révélé que ce chiffre devrait passer à 100 % d’ici 1 an !
Autre spécialité de l’entreprise : les vis de guidage destinées à intégrer des capteurs dans la boîte crânienne en vue du traitement de l’épilepsie. Ces vis doivent être fabriquées avec une extrême précision afin de garantir le positionnement exact du capteur. Décolletées, elles subissent ensuite plusieurs fraisages afin de permettre le passage d’une petite clé pour les fixer. L’état de surface à l’intérieur doit être impeccable de manière à pouvoir également les nettoyer plus facilement. « Certaines de ces vis exigent un perçage d’1 mm de diamètre sur une longueur de 20 mm, ce qui est extrêmement complexe à réaliser sur du titane. Cela implique beaucoup de savoir-faire que nous développons au quotidien, » précise Yannick Robichon. A titre d’exemple, DDLG a mis au point un process délicat, en collaboration avec son client, afin que les arêtes des vis soient suffisamment coupantes pour traverser la boîte crânienne mais pas trop pour éviter le risque de détachement de petites particules de titane au moment de l’insertion ou du retrait.
Pour ce même client, DDLG usine également les bouchons en plastique biocompatible qui évitent les fuites de liquide céphalorachidien. Là aussi DDLG a co-développé une technique de fabrication innovante qui empêche la formation de bavures susceptibles de se libérer dans le crâne du patient.
Bientôt un bureau d’études intégré
Si les connecteurs pour respirateurs ont été réalisés sur plan pour des raisons de délai, DDLG intervient souvent dès la phase de conception. Cela lui permet de trouver, en collaboration avec son client, le design de la pièce qui répondra le mieux à l’usage attendu et qui sera le moins complexe à produire. « Aujourd’hui, la demande de nos clients se résume de plus en plus fréquemment à une fonction, affirme Yannick Robichon. Il leur importe peu de savoir quel procédé d’usinage il faudra mettre en œuvre ; à nous d’apporter notre valeur ajoutée pour permettre l’industrialisation du produit. »
Face à cette évolution, DDLG a décidé de monter son propre bureau d’études, un projet qui devrait voir le jour prochainement.
Un choix stratégique délibéré
Le médical représente aujourd’hui 20 % de son activité mais l’objectif de Yannick Robichon est de dépasser les 50 %. Pour cela, il a déjà réservé un terrain auprès de la Communauté de communes Loue-Lison pour construire un bâtiment neuf où il intègrera un parc machines entièrement consacré à ce marché mais aussi une salle blanche, un investissement qui lui semble impératif sur le long terme. De la même façon, il avait anticipé il y a 5 ans la nécessité d’obtenir la certification ISO 13485, une décision dont il se félicite aujourd’hui. Pour lui, il n’y a pas de demi-mesure possible : si on choisit de travailler pour l’industrie du dispositif médical, on doit s’y lancer à fond. Sur ses 35 décolleteuses à commande numérique, la moitié sont déjà dédiées à cette clientèle. Elles ont toutes entre 6 et 9 axes, ce qui couvre un large panel de possibilités d’usinage. « Nous avons même changé notre huile de coupe pour la remplacer par une huile végétale que nous avons fait valider par l’INRS à Paris », précise-t-il.
Basée à Ornans à une vingtaine de kilomètres de Besançon, l’entreprise, qui emploie 35 personnes dont 3 apprentis, réalise un chiffre d’affaires annuel de 3 millions d’euros.