Coulée sous vide pour la production de pièces en petites séries
La coulée sous vide a beaucoup à offrir à la medtech : flexibilité de la conception, prix abordable et délai de mise sur le marché réduit. Materialise utilise cette technologie pour aider ses clients, comme ici Airinspace, à innover rapidement et à réagir aux augmentations urgentes de la demande.
Certaines technologies ont la vertu de stimuler les innovations et répondre aux changements dans une industrie en constante évolution comme la medtech. C'est le cas de la fabrication additive mais aussi du moulage sous vide. Synonymes de flexibilité, ces technologies offrent en effet une grande liberté de conception à laquelle s'ajoute un vaste choix de matériaux de haute qualité et de degrés de finition. Des qualités qui permettent de répondre aux besoins de nombreux types de dispositifs médicaux.
Pourquoi choisir la coulée sous vide ?
Comme pour tout projet de fabrication, le choix de la bonne technologie est essentiel. Lorsqu'elle est utilisée pour la production de petites séries, la coulée sous vide est plus rapide et plus viable financièrement que les technologies de production comparables telles que le moulage par injection, tout en offrant une finition comparable pour garantir la nettoyabilité.
« Cette technologie est idéale pour les commandes d'environ 100 pièces », explique Jiri Pinkas, technicien CAO et ingénieur de processus chez Materialise. « Parmi ses nombreux avantages figure la possibilité d'intégrer des inserts filetés et d'autres assemblages ».
La polyvalence est essentielle
L'un des principaux atouts de la coulée sous vide est la polyvalence de son processus de conception, qui accroît considérablement le potentiel d'innovation des produits. Contrairement à de nombreuses autres technologies, les clients peuvent demander des modifications du moule, comme des ajustements de détails mineurs dans la conception, même au milieu d'un projet. La différence réside dans la construction du moule. Réalisé en silicone, il peut être créé en deux jours et séparé en deux parties en raison de la flexibilité du matériau. Les moules en aluminium utilisés pour le moulage par injection peuvent nécessiter des mois de fabrication et doivent être divisés en plusieurs parties démontables en raison de leurs contre-dépouilles.
Cette technologie se distingue également par un choix particulièrement large de finitions, notamment en matière de peinture, avec différentes textures, des surfaces brillantes ou translucides, des options mates et satinées, pour n'en citer que quelques-unes.
Face à une augmentation soudaine de la demande : l'exemple d'Airinspace
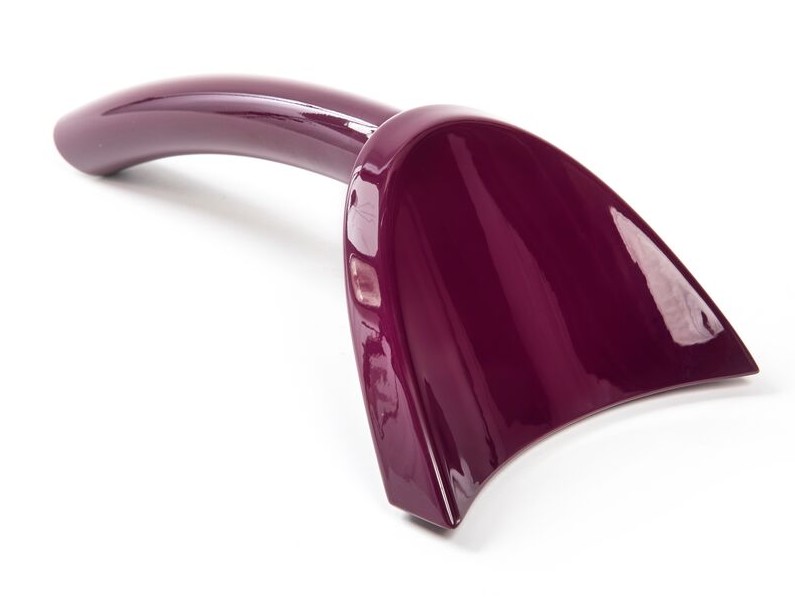
La peinture brillante est une des nombreuses options de finition disponibles pour le moulage sous vide (crédit photo Materialise).
Dans certains cas, ces avantages deviennent cruciaux, comme dans celui du fabricant français Airinspace. Depuis 2014, Materialise fournit des services de moulage sous vide pour deux pièces du système RHEA Cubair de l'entreprise : un équipement de désinfection par brouillard sec qui aide à stériliser les installations médicales.
« Nous avons choisi de travailler avec Materialise parce que l'entreprise est très bien placée sur le plan tarifaire tout en offrant une excellente assistance commerciale et technique », explique Nicolas Klaczynski, responsable du développement des produits chez Airinspace. « Nous leur commandons principalement des pièces impossibles à fabriquer avec les techniques traditionnelles, comme notre buse de distribution de produits brevetée, fabriquée par frittage de poudre."
Si la plupart des commandes concernent la production de faibles volumes, la pandémie de COVID-19 s'est traduite par une augmentation soudaine et urgente de la demande, en février et mars 2020. A cette époque, le gouvernement français a en effet passé une commande importante qui a fortement sollicité la chaîne d'approvisionnement d'Airinspace.
Au cours de ces deux mois, Materialise a dû produire plus de 1000 pièces dans des délais très courts. Le défi a pu être relevé en mettant sur pied une équipe de production spécialisée, en suivant une procédure normalisée pour garantir la conformité et en produisant plusieurs moules supplémentaires pour réduire les délais.
« Au fil des ans, Materialise nous a aidés à optimiser nos pièces pour obtenir une production fiable et respecter nos besoins de performance », déclare Nicolas Klaczynski. « Nous exigeons également la traçabilité des lots de fabrication, que nous avons mise en œuvre ensemble. Lorsque nous leur avons soumis cette demande, ils ont réagi immédiatement et les résultats ont été à la hauteur de nos attentes ».
« Les pièces que nous fabriquons pour Airinspace sont recouvertes d'une couche de finition très brillante et nous y intégrons des inserts filetés », explique Pinkas. « Ils n'ont donc pas besoin de s'adresser à plusieurs entreprises différentes ».
Coulée sous vide : un procédé en six étapes éclair
« Comme toutes les pièces moulées sous vide, les pièces d'Airinspace sont produites en suivant un processus soigneusement contrôlé en six étapes », explique Jiri Pinkas. « Nous commençons toujours par évaluer la faisabilité avec le client pour voir si nous pouvons recourir à cette technologie », explique Jiri Pinkas.
La coulée sous vide consistant à copier un modèle physique, la deuxième étape est destinée à créer le maître-modèle, ou patron : une copie imprimée en 3D de la pièce originale. Celle-ci est à son tour utilisée pour créer un moule en silicone. Les pièces sont ensuite coulées dans ce moule, puis soumises à un post-traitement qui les prépare à la peinture : une couche d'apprêt et une couche de finition brillante, ainsi que toute demande supplémentaire, telle que l'intégration d'inserts filetés.
« C'est un processus assez rapide », souligne Jiri Pinkas. « L'évaluation de faisabilité dure environ une journée. À partir du moment où un client passe une commande, il nous faut environ six jours pour fabriquer le modèle imprimé et les moules. Ensuite, cela dépend du nombre de pièces dont le client a besoin, mais nous pouvons toujours produire davantage de moules pour accélérer le processus ».
« Dans ce cas, la coulée sous vide était indubitablement le bon choix », ajoute Jiri Pinkas. « La technologie RIM et le moulage par injection auraient également fonctionné, mais pour un coût nettement plus élevé et des options de post-traitement moins nombreuses. Cela aurait représenté davantage de travail, sans parler de la nécessité pour Airinspace de confier les finitions dont il avait besoin à d'autres sous-traitants ».