Moulage dynamique : un moyen inédit de produire des DM personnalisés
A la croisée de l'impression 3D et du moulage par injection, le procédé développé par 3Deus Dynamics permet de produire des pièces en polymère sans reformulation chimique, sans structure support et sans limite de géométrie. Premier marché visé : les pièces médicales en silicone de forme complexe.
Le moulage par injection est un procédé classique pour la fabrication de pièces industrielles. Il offre deux avantages majeurs : de fortes cadences de production et une compatibilité avec la plupart des matériaux usuels, au premier rang desquels figurent les polymères. Mais la principale limite du moulage par injection demeure la production de formes complexes.
Quant à la fabrication additive, elle s’est développée plus récemment et rapidement avec l'avantage d'une production de pièces personnalisées, très intéressante pour un large éventail de secteurs comme l’aéronautique, le luxe, l’agro-alimentaire, le transport… et bien entendu le médical. L’impression 3D évolue très rapidement avec des technologies toujours plus sophistiquées et innovantes telles que la stéréolithographie, permettant d’imprimer de plus en plus de matériaux disponibles sur le marché (résine, métaux, céramiques, silicones…).
Cependant, l’impression 3D reste encore limitée en termes de complexité de design, de cadence de production et de compatibilité matière.
En effet, dans la grande majorité des cas, une reformulation chimique des matériaux usuels de l’industrie manufacturière est nécessaire pour les rendre compatibles avec les procédés d’impression 3D. Dans le domaine de la santé, l’utilisation de la fabrication additive reste donc restreinte à des formes relativement simples et à des matériaux facilement imprimables sans modification de formulation. D'autant que cette modification, quand elle est nécessaire, implique une revalidation réglementaire des matières et donc des coûts associés importants pour les industriels.
Une technologie française brevetée et récompensée au concours i-Lab
Appelé "moulage dynamique", le procédé développé par 3Deus Dynamics permet de lever des verrous industriels et d’accéder à de nouveaux marchés jusqu’à alors limités pour les techniques classiques d’impression 3D par dépôt de matière ou de moulage par injection. Au croisement des deux approches, il en combine les avantages, proposant une nouvelle façon de produire des pièces techniques complexes et à des cadences de production élevées.
La technologie a été mise au point au sein de la plateforme technologique 3d.FAB (Université Lyon1 / CNRS) et a fait l’objet du dépôt de deux brevets.
La création de 3Deus Dynamics, fin 2020, a pu se faire grâce à un programme de maturation de la SATT Pulsalys Lyon-Saint Etienne, et à l’accompagnement de l’industriel Elkem Silicones. 2021 aura été marquée par une levée de fonds d'amorçage de 700 000 €, une place parmi les lauréats du concours national d’innovation i-Lab et l'obtention d'une Bourse French Tech Emergence.
Un procédé hybride précis et rapide
Le moulage dynamique utilise les propriétés d’écoulement des matériaux fluides et granulaires pour la fabrication de produits aux caractéristiques géométriques complexes à haute valeur ajoutée.
Le fluide est déposé par un micro-doseur, qui est lui-même immergé au sein d’un milieu granulaire. Celui-ci forme alors un moule supportant le matériau pendant l’impression. C’est à ce stade que le moulage dynamique se différencie des autres technologies.
Les propriétés physiques de la poudre utilisée permettent non seulement de supporter la pièce imprimée durant toute la phase de fabrication, mais aussi de se reformer après chaque mouvement du micro-doseur.
La résolution d’impression peut atteindre une dizaine de micromètres avec une cadence proche d’un litre par heure. L’un des avantages majeurs de ce procédé est de permettre l'utilisation des matériaux usuels du moulage par injection, comme le silicone liquide (LSR), sans reformulation chimique.
Par ailleurs, l’utilisation d’un milieu granulaire en tant que moule dynamique permet de s'affranchir de la fabrication d'un moule classique qui bien souvent est longue et coûteuse.
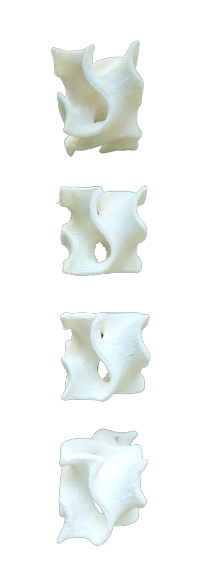
Gyroïdes en silicone obtenus par moulage dynamique, avec des duretés de 10, 50, 60 et 70 Shore A (de bas en haut).
Le moulage dynamique se distingue enfin par une possibilité intéressante : celle pour la poudre de se mélanger de manière contrôlée au matériau injecté afin de fabriquer un composite. Cela permet de fonctionnaliser la pièce avec, par exemple, des propriétés électriques, magnétiques ou encore antimicrobiennes.
Priorité aux DM en silicone
Ce nouveau procédé s’adresse à tous les secteurs d’activité mais 3Deus Dynamics souhaite avant tout s’imposer comme un acteur majeur du développement de dispositifs médicaux pour la médecine personnalisée.
S'il est possible d'utiliser tous les polymères disponibles sur le marché, la première offre est centrée sur la fabrication de pièces en silicone. Des milliers de formulations existent sur le marché, utilisées dans tous les secteurs industriels. Mais une très faible part de ces silicones est aujourd'hui compatible avec l'impression 3D pour la mise en œuvre de pièces complexes.
Or, sur le marché de la santé en particulier, la demande est forte pour des pièces en silicone de formes complexes : modèles anatomiques, implants auditifs, prothèses, orthèses... Le moulage dynamique permet notamment de travailler avec une large gamme de silicones présentant des duretés allant de 0 à 90 Shore A.
L’intégration de ces élastomères rend possible la réalisation de répliques physiques durables, aux propriétés mécaniques et géométriques fidèles, permettant par exemple de mimer des tissus mous sains ou pathologiques tels que le foie, les reins et les artères.
3Deus Dynamics travaille actuellement pour des industriels, cliniques ou hospitaliers afin de concevoir des dispositifs médicaux de toutes classes.
La validation des couples matériaux-poudres selon la norme ISO 10993 est en cours de réalisation afin de confirmer la biocompatibilité des dispositifs produits par moulage dynamique. 3Deus Dynamics vise également une certification ISO 13485 au 1er semestre 2022.