Des paniers de stérilisation « Swiss made » réalisés à la carte
Fort d’une vingtaine d’années d’expérience dans ce domaine, Pierre-Louis Beaud dirige la société Inomed Technology, qui conçoit et fabrique des paniers de stérilisation sur mesure pour l'instrumentation spécifique de chaque fabricant d’implants. Si ces produits sont a priori simples à réaliser sur le plan technique, ils nécessitent pourtant un soin très attentif pour garantir la sécurité du patient et répondre aux attentes des utilisateurs.
Par Evelyne Gisselbrecht, DeviceMed
Monsieur Beaud, pourriez-vous nous résumer l’histoire de la société Inomed Technology ?
J’ai créé Inomed Technology avec deux associés en 2008, après avoir dirigé pendant 5 ans la filiale européenne de Riley Medical, fabricant américain de paniers de stérilisation. Cette décision a fait suite au rachat de ce groupe par Symmetry Medical et à la fermeture du site suisse. Si au départ nous avions envisagé la fabrication d’instruments médicaux, nous nous sommes très vite recentrés, à la demande de nos clients, sur notre métier de départ : la conception et la fabrication de paniers de stérilisation pour le compte des fabricants d’implants en orthopédie, rachis, traumatologie et extrémités. Inomed Technology est implantée à Courtelary, à une vingtaine de kilomètres de Bienne, à proximité des sièges européens des grands fabricants d’implants tels que Stryker, Johnson & Johnson, Zimmer Biomet, Depuy Synthes…
Aujourd’hui, je suis seul à diriger Inomed Technology.
Vous vous définissez à la fois comme un fabricant de paniers de stérilisation et comme une société de services. Qu’entendez-vous par là ?
En tant que fabricant de paniers, nous intervenons en bout de chaîne : nos clients développent d’abord leurs prothèses, puis leurs instruments. Ils font ensuite appel à nous, étant entendu que la commercialisation de leurs produits ne doit surtout pas être ralentie par un quelconque problème au niveau des paniers. Nous travaillons en étroite collaboration avec nos clients pour élaborer le panier qui correspond le mieux à leurs besoins, dans le délai le plus court possible. Nous pouvons réaliser un projet de A à Z dans un délai de 6 à 8 semaines, alors qu’il faut plus de 6 mois à certains de nos concurrents. Nous offrons à nos clients la réactivité et la flexibilité d’une petite entreprise et sommes très probablement les plus rapides du marché.
Par "services", nous entendons aussi la garantie de la qualité et de la stérilisabilité de nos produits, qui ne doivent en aucun cas constituer une barrière à la stérilisation des instruments. Nos paniers sont des dispositifs médicaux de classe I, nous sommes audités annuellement par l'organisme de certification BSI. Nous disposons de la certification ISO 13485 et sommes enregistrés auprès de la FDA. Nous fournissons à nos clients l’ensemble des dossiers techniques nécessaires à l’obtention de leur marquage CE.
Vos paniers de stérilisation sont pour 95 % d’entre eux réalisés sur mesure. En quoi les attentes diffèrent-elles d’un client à l’autre ? Comment y répondez-vous ?
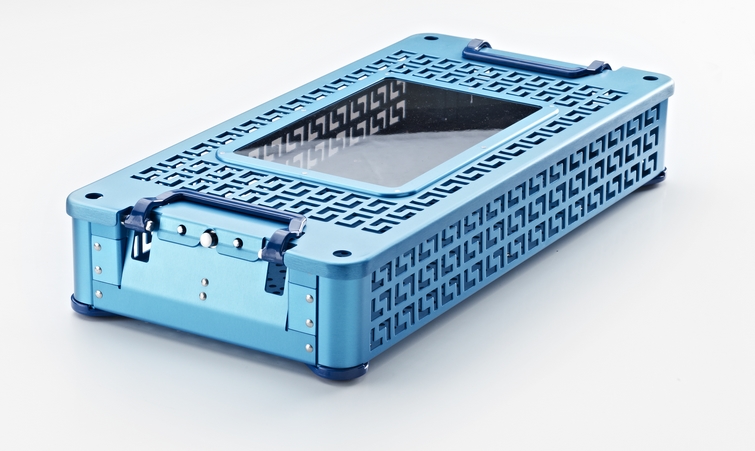
Dans le système "à la carte", le client peut tout choisir en fonction de ses exigences : de la fermeture aux poignées, en passant par les supports, la forme des trous ou, ici, la couleur des composants.
Un panier remplit essentiellement quatre fonctions : ranger les instruments, les transporter, les stériliser et permettre au chirurgien de reconnaître le fabricant de prothèses. Or, ces exigences sont souvent contradictoires. Par exemple, pour certains clients, l’essentiel est de pouvoir loger le plus d’instruments possibles dans le plateau, ce qui va augmenter son poids et compliquer la stérilisation. Notre rôle consiste à attirer l’attention du client sur ces différents points et à établir avec lui le cahier des charges le mieux adapté, sachant qu’il n’existe pas de panier répondant parfaitement à toutes les exigences.
Selon les marchés, les attentes peuvent s’avérer très différentes. En Angleterre par exemple, les fabricants d’implants accordent une grande importance au poids des bacs. En Allemagne, le critère essentiel demandé est la lavabilité du panier, alors qu’en Italie, les clients mettent l’accent sur sa résistance mécanique. Certains clients favoriseront davantage le design de leur plateau, sa couleur, etc. Nous nous adaptons à leurs souhaits tout en les conseillant objectivement sur la base de notre expertise.
En général, lorsque nous rencontrons un prospect pour la première fois, nous emportons avec nous tout un panel de paniers différents à partir duquel le prospect pourra choisir le type de fermeture, les poignées, les supports ou encore les couleurs qui lui conviennent. Nous appliquons le principe de choix à la carte et définissons avec le client un type de plateau qu'il utilisera ensuite pour tous ses projets afin d'assurer une uniformité de style.
Quels matériaux utilisez-vous ?
Nous fabriquons l'essentiel de nos caisses en acier inoxydable 304 (1.4301). On voit d’ailleurs de moins en moins de bacs thermoformés sur le marché car ils présentent deux défauts majeurs : ils se cassent facilement et causent des problèmes de rétention d'eau.
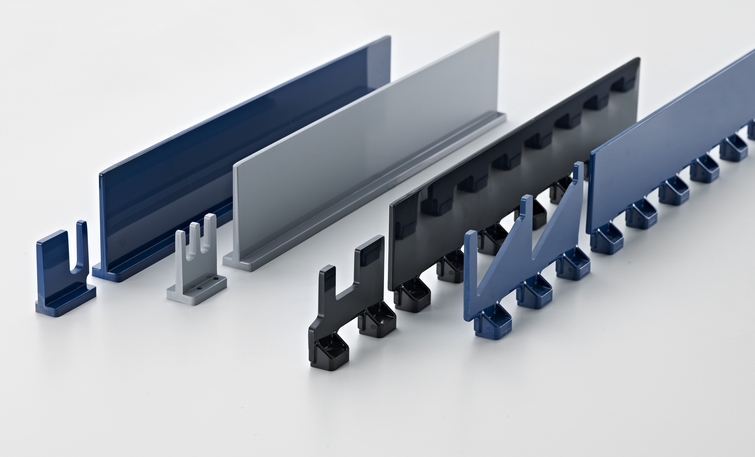
Inomed Technology privilégie les supports réalisés en plastique dur de type PPSU (Radel) pour les instruments de grande taille et en silicone pour les petits instruments.
Pour nos supports, nous privilégions le plastique plutôt que le métal, de manière à éviter de rayer les instruments. Bien que certains de nos confrères utilisent des supports en acier revêtu de Rilsan, nous demeurons sceptiques quant à la biocompatibilité de ce type de revêtements et ne voulons prendre aucun risque. Pour les instruments les plus lourds, nous préconisons les supports en plastique dur de type PPSU (Radel). Cela évite de trop serrer les instruments - ce qui pourrait avoir une incidence sur la stérilisation -, tout en les maintenant correctement. Pour les instruments de plus petite taille, nous recommandons des supports en silicone. Afin d'éviter tout résidu d'huile de coupe qui risquerait de contaminer les instruments, tous nos supports sont usinés à sec.
Je précise que les matériaux utilisés sont testés à 100 % et que nous gardons bien évidemment tous les certificats matière correspondants.
En quoi vous distinguez-vous de vos concurrents sur le plan de la conception et de la fabrication de vos paniers ?
Pour pouvoir garantir à nos clients la qualité de nos paniers et leur assurer le meilleur délai possible, nous avons fait le choix de réaliser l'ensemble de la conception et de la fabrication en interne. Nos paniers sont exclusivement Swiss made. La phase de développement constitue l’essentiel du travail : le client nous fournit le fichier 3D de ses instruments et nous concevons un plan d’agencement (layout) en CAO. Comme notre atelier d’usinage est situé au rez-de-chaussée et notre bureau d’études à l’étage, nous validons la fabrication de nos paniers au fur et à mesure et procédons aux modifications nécessaires en temps réel. Nous testons tous les prototypes directement chez nos clients, en nous assurant avec eux que les instruments sont bien tenus, qu’ils ne se touchent pas et qu’ils peuvent être stérilisés correctement. Ensuite, nous réalisons un « samba test » : nous retournons vigoureusement le panier dans tous les sens puis nous vérifions que son contenu est resté parfaitement en place.
Tous nos paniers sont testés et validés à 100% et nous en garantissons l’excellence. Nous proposons aussi à nos clients qui le souhaitent d’organiser des tests de validation de stérilisation complets des ancillaires. C’est un service complémentaire qui est généralement très apprécié.
Pouvez-vous nous dire quelques mots sur votre gamme Stack Line ?
Il s’agit de paniers empilables qui sont accrochés les-uns aux autres et sont fermés par un couvercle unique sur le dessus. Ils répondent aux attentes actuelles de réduction du volume occupé par les ancillaires dans les blocs opératoires. Comme pour tous nos produits, les poignées sont attachées directement au bac, ce qui empêche les paniers de tomber s’ils sont mal fermés.
Pouvez-vous nous citer certaines innovations introduites par Inomed ?
Inomed en bref
- un peu plus d'une vingtaine d’employés au total
- 4 personnes au bureau d’études
- 1500 m² d’ateliers de production
- Clientèle située principalement en Europe Occidentale : Suisse, France, Allemagne, Italie, Royaume-Uni
Nous avons inventé une dizaine de systèmes de fermeture tels que le T-Latch, un bouton pression monté sur une tôle en acier ressort. De nombreux confrères nous ont copiés depuis. Nous avons également développé des racks à vis sur mesure pour les besoins de la traumatologie. Par ailleurs, nous avons mis au point des accessoires pour tenir des petites pièces ou des instruments très spécifiques, notre but étant d’avoir une solution à proposer quel que soit le type d’instruments. Enfin, nous pouvons aujourd'hui livrer des couvercles dont les quatre coins soient parfaitement fermés, comme s'ils étaient emboutis.
Nous avons également créé nos propres vis de montage de manière à éviter aux chirurgiens tout risque de coupure et de déchirure.
Vous contrôlez vos paniers à 100 %. Quels moyens utilisez-vous ?
Nous avons développé en interne un système de contrôle "photographique" ScanVision de nos paniers assemblés. Le plateau est placé dans un boîtier puis est comparé à un modèle de référence par le biais d’un logiciel qui détecte toutes les différences. Au contraire des contrôles purement visuels, la parfaite fiabilité de ce procédé électronique permet d'assurer que 100 % des paniers sont conformes aux plans.
[Source des illustrations : Inomed Technology]