Usinage de pièces microscopiques pour le médical
Les exigences particulières de l'Américain Medical Micro Machining en matière de micro-usinage de composants médicaux ont amené le constructeur Microlution à développer une nouvelle plate-forme de centre de tournage multifonction (MR-4) dédiée à la production de pièces minuscules.
Comme on pourrait le deviner, Medical Micro Machining est spécialisé dans la production, par usinage, de prototypes et de petites séries de très petits composants, principalement pour le secteur médical. Ce dernier représente 70 % de l'activité de l'entreprise.
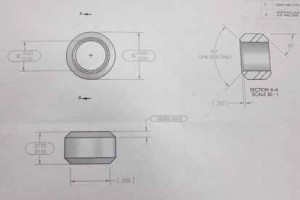
Difficiles à photographier tellement elles sont minuscules, les pièces produites peuvent présenter des tolérances de l'ordre de 2,5 microns.
Son président, Rob Whitmore, souligne que les deux principaux défis auxquels fait face l'atelier sont la miniaturisation et le recours à des matériaux atypiques. Par miniaturisation, on entend des pièces comme celle dessinée ci-contre : un élément de tube présentant, comme dimensions maximales, une longueur de 4,3 mm, un diamètre interne de 400 microns, un diamètre externe de 660 microns, et de minuscules chanfreins internes et externes. Côté matériaux, certaines pièces exigent des plastiques biorésorbables, des plastiques aux propriétés magnétiques, du tungstène-cuivre, du titane, etc.
Ces défis fondamentaux ont modelé le type d'équipement dont a dû se doter Medical Micro Machining au fil des années et les processus qu'il a fallu développer pour usiner des pièces avec des tolérances de l'ordre de ±2,5 microns. En fin de compte, cette démarche a mené à la conception d'un nouveau type de plate-forme d'usinage par micro-tournage que l'atelier utilise en conjonction avec des tours automatiques pour réaliser le tournage, le meulage et le perçage, avec l'objectif d'usiner des pièces microscopiques à partir d'une barre en un seul réglage.
Une histoire de vis biorésorbable congelée
En 1994, Rob Whitmore fonde Medical Micro Machining avec sa femme Kathy et son partenaire Ed Freer dans la Simi Valley, en Californie. À l'époque, l'entreprise présente deux visages. M. Freer se concentre sur la fabrication et la vente d'une gamme de centres de micro-tournage référencée AM-2000, tandis que le couple Whitmore gère une activité d'usinage en sous-traitance.
M. Whitmore précise que l'élément déclencheur de l'essor de cette activité de sous-traitance a été le développement d'un procédé pour l'usinage de vis à os biorésorbables à partir d'un plastique qui se dégrade au fil du temps. À cette époque, ce matériau ne pouvait pas être produit par moulage par injection. Avec un point de fusion d'environ 55°C, il oblige Rob Whitmore à concevoir une opération d'usinage employant de l'azote liquide pour congeler le matériau juste avant la découpe. Dès lors, l'activité d'usinage en sous-traitance entame une croissance régulière et l'atelier commence à recevoir des demandes de production de pièces dans d'autres matériaux problématiques.
Au décès de M. Freer en 2007, le couple Whitmore décide de maintenir la société mais en se concentrant uniquement sur l'activité d'usinage en sous-traitance. Il transfère alors la société dans la ville natale de M. Whitmore, à Colfax dans l'état de Washington. L'atelier continue d'utiliser certaines machines originales AM-2000, mais entame la recherche d'un équipement alternatif lorsque ces machines commencent à tomber en panne plus fréquemment. A l'époque, Rob Whitmore ne parvenait pas à trouver de modèles de machines similaires aux AM-2000. Toutefois, après la découverte des équipements de micro-meulage et d'usinage au laser fabriqués par Microlution (Chicago, Illinois), il contacte le constructeur avec l'idée de créer une machine de micro-tournage semblable à l'AM-2000.
Quelques années de développement plus tard est né le modèle MR-4 : un micro-tour 4 axes à outils multiples offrant des fonctionnalités adaptées aux opérations de tournage, meulage et perçage de très petites pièces.
Medical Micro Machining est ainsi devenu l'atelier de beta-test pour cette nouvelle ligne de machines de Microlution, avec les quatre premiers modèles construits. Ces machines compactes ont une base en béton polymère de 254 mm qui absorbe les vibrations 20 fois plus efficacement que l'acier. Montés au-dessus du bâti, les axes X, Y et Z fournissent une précision de position de l'ordre de 1 micron. La machine offre un volume de travail XYZ de 300×125×150 mm et accepte des barres d'un maximum de 7,9 mm de diamètre.
Un palpeur pour accélérer les configurations
Rob Whitmore dit apprécier deux fonctionnalités importantes qui sont la configuration d'outil automatisée via un palpeur Blum et la précision du mouvement de l'axe Y. Le palpeur peut mesurer automatiquement la longueur des outils, ce qui réduit considérablement les délais de configuration par rapport aux méthodes manuelles. Cette capacité est particulièrement précieuse pour les ateliers tels que celui de Medical Micro Machining qui réalise principalement des prototypes et des petites séries, nécessitant des changements de configuration fréquents, contrairement aux gros volumes de production. Concernant l'axe Y, sa position peut être réglée avec une précision de l'ordre de 2,5 à 5 microns par rapport à la ligne centrale de la pièce. Lorsqu'un atelier travaille sur des pièces plus grandes, il peut se permettre une tolérance d'une cinquantaine de microns, mais dans le cas de Micro Medical Machining, 50 microns représentent précisément la taille de certaines pièces à usiner.
L'axe Y permet également d'empiler jusqu'à quatre outils dans un seul porte-outil, chacun d'eux pouvant être enclenché durant les configurations à l'aide du palpeur. L'atelier possède également cinq broches rotatives installées sur la plaque porte-outil pour réaliser le meulage et les opérations associées. Après l'usinage, la séparation et la dépose de chaque pièce dans un collecteur automatique, un tire-barre pneumatique installé sur la plaque porte-outil amène automatiquement une portion neuve de barre dans la zone de travail pour l'usinage de la pièce suivante.
Un contrôle par caméra vidéo
Les machines MR-4 intègrent également une caméra vidéo avec agrandissement 13x et un moniteur dédié. Rob Whitmore déclare que cela s'avère particulièrement bénéfique durant les configurations, notamment avec les très petits outils utilisés ou dans le cas d'une configuration inhabituelle.
La caméra permet aussi d'observer les opérations d'usinage en temps réel. Même si cette fonction n'est pas très utile lors de l'utilisation de liquide de refroidissement, elle peut être précieuse lors de l'usinage à sec de pièces en plastique, par exemple. L'opérateur peut ainsi voir si une mèche est mal alignée et oscille, déterminer les raisons d'empreintes étranges sur les pièces usinées, etc. Il en va de même avec l'usinage à sec du laiton, un matériau que l'atelier emploie parfois afin d'établir initialement une configuration pour les travaux qui demandent un métal plus coûteux et exotique.
Un atelier segmenté
L'atelier de Medical Micro Machining est divisé en deux zones de production : une pour l'usinage à sec (principalement pour les plastiques de qualité médicale pouvant être facilement contaminés) et l'autre qui emploie un liquide de refroidissement à base d'huile minérale. Actuellement, deux des machines MR-4 sont disposées dans le segment sec et les deux autres se trouvent dans le segment humide.
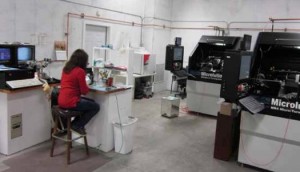
Les deux MR-4 sur le segment sec de l'atelier sont principalement employées pour usiner des capsules en plastique intégrées dans un DM.
L'utilisation des MR-4 sur le segment sec concerne principalement l'usinage de capsules en tube plastique utilisées pour un dispositif médical qui surveille les niveaux de glucose d'un patient en continu. Les capsules avaient a priori besoin d'un polissage après le tournage de façon à être parfaitement transparentes. Mais l'utilisation d'un outillage au diamant et d'un processus de tournage que M. Whitmore n'a pas voulu révéler, a éliminé la nécessité de cette opération de polissage. Les bouchons de ces capsules sont également fabriqués dans cette zone sur l'une des machines AM-2000 restante. A noter que l'atelier usine les bouchons en utilisant les restes de barres utilisées sur les machines MR-4. Cela permet d'utiliser 95 % de chaque barre achetée.
En plus d'une MR-4, le segment humide comprend quelques tours automatiques, y compris le modèle Eco 10a de Tornos. L'atelier utilise également cette machine pour les très petites pièces. La décision d'utiliser la MR-4 ou les tours automatiques dépend en grande partie de la taille du lot. Si une production ne demande que 50 à 100 pièces, elles seront vraisemblablement produites sur la MR-4 car les temps de configuration sont plus rapides. Inversement, il est plus avantageux de configurer un tour automatique lorsque les lots sont plus volumineux. Dans certains cas, toutefois, il peut être préférable de configurer un travail de création de prototype sur un tour automatique s'il est évident qu'une production substantielle suivra.
La machine Eco 10 est d'ailleurs équipée d'un dispositif unique de collecte de pièces minuscules, conçu par Medical Micro Machining. Lorsqu'un composant est détaché de la barre, un système de vide l'aspire dans un tube passant à travers la contre-broche et dans un panier à mailles fines.
De nouvelles machines à l'horizon
Les quatre machines MR-4 installées chez Medical Micro Machining représentent la conception originale de Microlution pour cette plate-forme de micro-tournage. Le constructeur a depuis modifié sa machine grâce aux retours de Rob Whitmore. Celui-ci prévoit d'ailleurs l'acquisition de l'une des nouveaux modèles pour remplacer une machine actuellement utilisée dans le segment humide de l'atelier (machine qui sera nettoyée et transférée au segment sec).
Les capacités d'inspection de l'atelier seront également mises à niveau étant donné que la mesure des micro-pièces peut être aussi difficile que leur usinage.