Polissage éclair et automatisé du composant fémoral des prothèses de genou
Otec développe des équipements de tribofinition avec une technologie adaptée aux besoins des fabricants d'implants. Elle permet d’obtenir un poli miroir avec une rugosité finale inférieure à 0,020 μm en quelques minutes, en une seule passe, sur des prothèses à charnière ou à glissement en titane ou en CoCr.
Le marché hautement concurrentiel des implants orthopédiques est détenu à 85 % par 5 grands fabricants, tandis que quelque 200 autres sociétés se disputent la part restante. La concurrence étant rude, les sociétés cherchent continuellement des moyens plus rentables et surtout plus rapides pour fabriquer leurs implants.
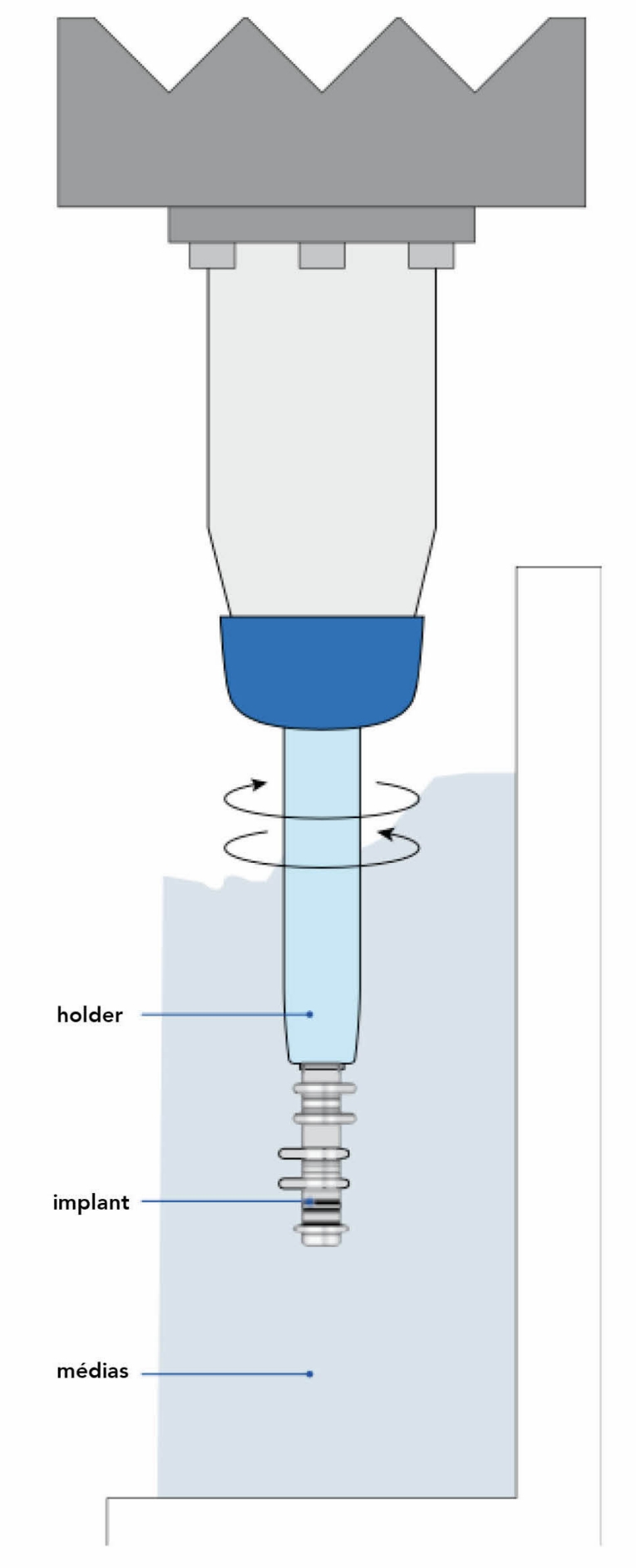
Le média est projeté à près de 40 G sur la surface des pièces grâce à une accélération de la broche à 2000 tr/min en 0,5 s.
La vitesse de traitement est l'un des principaux atouts de la technologie SF Pulsfinish mise au point et brevetée par Otec, fabricant allemand distribué en France, en Suisse et au Luxembourg par Hauswirth S.A.S. Cette technologie de polissage à flux continu a ouvert la voie à une nouvelle génération de machines de finition hybrides, combinant les avantages de la tribofinition et de la smuritropie. Ces équipements répondent aux exigences de vitesse des productions d'implants en grandes séries.
Le principe est simple : exercer le maximum de force sur les pièces à traiter en densifiant le média, de façon à obtenir une abrasivité maximale et un process le plus court possible. Les machines de la série SF sont dotées d’une cuve de maximum 220 litres, dans laquelle les médias abrasifs sont densifiés artificiellement par force centrifuge à raison de 80 à 110 tr/min. Les implants sont placés dans ce flux d’abrasifs via un système de broches. Celles-ci disposent d’une amplitude angulaire jusqu’à -35° en plus d’une rotation continue ou par séquençage, pour optimiser le contact des médias avec les implants.
Dans le cas des prothèses totales de genoux, cela permet de traiter l’intégrabilité de la box des pièces fémorales. Grâce à la technologie SF Pulsefinish, le média est projeté à près de 40 G sur la surface des pièces grâce à une accélération de la broche à 2000 tr/min en 0,5 s, puis les pièces sont éjectées dans le sens inverse avec les mêmes paramètres. La répétition de ce mouvement alterné permet de polir l’intégralité de la box là où les systèmes de polissage robotisés avec disques en cisaille ou en flanelle montrent des difficultés d’accès incontournables.
De cette façon, Otec rend le process stable et reproductible en supprimant les problématiques chroniques de réglage des robots de polissage et de nettoyage des surfaces fortement polluées par les abrasifs en pâte. Le système intègre tout de même un robot développé conjointement avec l'intégrateur allemand FMB, mais celui-ci est uniquement destiné à l'approvisionnement et à la manipulation des prothèses lors d’un nettoyage par ultrasons post-polissage.
Cette technologie, signature du savoir-faire d'Otec depuis plus de 25 ans, permet d’obtenir un poli miroir avec une rugosité finale inférieure à 0,020 μm en quelques minutes, en une seule passe, sur des prothèses à charnière ou bicondyliennes en titane ou en CoCr. Ce procédé 100 % mécanique est également adapté au polissage des prothèses unicompartimentales (PUC).
Enfin, le procédé SF repose sur un traitement exclusivement mécanique, le média utilisé étant à base de céramique, de plastique ou de coquille de noix. Cette méthode ne nécessite pas de granulat d'acide ni d'électrolyte, ce qui réduit quasiment à néant le risque de dépôt de résidus cytotoxiques et garantit la biocompatibilité de l'implant.
La technologie SF Pulsfinish peut être mise à l'épreuve au sein du "Finishing Center" au siège d'Hauswirth, à Soultz Sous Forêts (67).
[Source des illustrations : Hauswirth]