Optimiser le traitement du plastique recyclé avec les canaux chauds
Concilier les produits médicaux à usage unique et le développement durable est une vraie gageure. Mais Heine Optiktechnik a relevé le défi en produisant des spéculums auriculaires avec une démarche originale de surcyclage et le recours à la technologie des canaux chauds de Günther Heisskanaltechnik.
Dédié à l’inspection de l’intérieur de l’oreille, l’otoscope est coiffé d’un speculum auriculaire (embout) qui peut être stérilisable (en inox) ou à usage unique (en plastique). La plupart des médecins préfèrent les spéculums jetables, plus rapides à remplacer après chaque examen.
Mais cela entraîne beaucoup de déchets dans les cabinets médicaux et les hôpitaux.
Une nouvelle vie pour les plastiques des vieux réfrigérateurs
Face à ce problème, le fabricant allemand d'instruments de diagnostic primaire, Heine Optiktechnik a décidé de mettre en place une démarche de surcyclage de ces spéculums auriculaires. Le surcyclage (upcycling en anglais) consiste à récupérer des produits usagés et de les transformer pour leur conférer une nouvelle utilité et leur assurer une qualité supérieure.
La bonne idée d’Heine a été d’utiliser du plastique provenant de vieux réfrigérateurs pour produire ses embouts à usage unique marqués AllSpec.
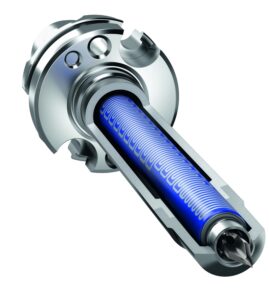
Moins gourmande en énergie et de petite taille, la buse de canaux chauds BlueFlow permet de générer une chaleur homogène au plus près du plastique sans pré-chauffage (crédit photo : Günther).
Grâce au recyclage contrôlé de ces réfrigérateurs, qui permet de capturer des gaz CFC nocifs pour le climat, l’entreprise "économise" 1 996 tonnes de CO2 par an.
« Bien entendu, nous avons testé minutieusement les embouts réalisés avec le plastique recyclé», explique Joachim Gutschka, responsable du développement des ressources chez Heine. « Il ne fait aucun doute qu'ils répondent à toutes les exigences du secteur des dispositifs médicaux ».
Durable jusque dans le procédé de production
Le projet global "Sustainable AllSpec Tips", qui s'est déroulé sur deux ans, ne se limitait pas au surcyclage du matériau. L'entreprise souhaitait également parvenir à un procédé de production aussi durable que possible. Elle a ainsi opté pour une presse à injecter électrique, avec un outillage adapté.
La mise au point de l'équipement complet a duré environ 5 mois, de la conception à la production. Le concept prévoyait une injection latérale et une commande séparée des points d'injection via des buses à canaux chauds. C’est à ce niveau que le fabricant a fait appel à Günther Heisskanaltechnik, spécialiste de la technologie des canaux chauds et froids dans l'injection plastique.
L'utilisation d'un système à canaux chauds apporte en soi un certain nombre d'avantages significatifs qui permettent à la fois de préserver les ressources, d'augmenter la qualité du produit et d'améliorer l’efficience de la production.
« En évitant des carottes de coulée inutiles, le rendement élevé de nos systèmes à canaux chauds permet d'économiser beaucoup de matières premières coûteuses », explique Horst-Werner Bremmer, responsable du conseil en technologie d'application chez Günther. « Des pièces parfaitement formées réduisent également le taux de rebut au minimum ».
Autre point positif en faveur de l’efficience de production, Günther a développé des buses économes en énergie basées sur une technologie propriétaire qui consiste à imprimer la résistance sur un tube en acier et à la recouvrir d'une couche très fine de céramique. C’est le cas ici avec les buses ouvertes de type 5SMF30K dotées d'éléments chauffants BlueFlow. Ces derniers se caractérisent par une épaisseur d'environ 20 μm, ce qui se traduit par un contrôle beaucoup plus précis de la répartition de la température dans l'ensemble de la buse. Le recours à la technologie BlueFlow permet d'obtenir une résistance beaucoup plus compacte, à savoir ici : 346 x 446 mm. Heine a pu ainsi utiliser la presse à injecter Allrounder 370 A d’Arburg, qui affiche des dimensions réduites.