Stratégies de test de fabrication pour les dispositifs médicaux connectés
Intégrer l'Internet des objet dans un dispositif médical représente un défi particulier pour son fabricant en matière de tests de fabrication. Keysight Technologies nous explique dans cet article les pièges à éviter et les stratégies à adopter pour limiter les risques de défaillances sur le terrain ainsi que le coût qu'elles entraînent.
Par Sook-Hua Wong, responsable Segment industriel, Keysight Technologies
Conjuguée aux attentes croissantes des patients, la hausse du coût des soins favorise l’adoption de l'Internet des objet (IoT) en santé, également appelé Internet des objets médicaux (IoMT pour Internet of Medical Things). Aujourd’hui, de nombreux dispositifs médicaux sont ainsi connectés à Internet, qu'il s'agisse de systèmes d’imagerie à ultrasons, de glucomètres, de stimulateurs cardiaques, de prothèses auditives, de systèmes de monitoring portés sur soi (wearables), etc. Grâce à ces solutions connectées, les patients dont l’état n’est pas critique peuvent rester à domicile, réduisant ainsi le nombre d’admissions à l’hôpital et les coûts afférents.
Mais au moment d’intégrer l’Internet des objets dans leurs produits, les fabricants de DM sont confrontés à des défis particuliers. Nombre d'applications réclament une fiabilité et une longévité à toute épreuve, une connectivité sans fil ininterrompue, et un fonctionnement parfaitement fluide dans les environnements physiques les plus difficiles. Face à de telles exigences, les fabricants sont dans l’obligation de recourir à des stratégies de test fiables et efficaces, et d'en optimiser le coût.
Des tests de fabrication souvent insuffisants
De nombreux DM font l’objet d’une caractérisation minutieuse au cours de la phase de conception afin de garantir leur qualité. En phase de fabrication cependant, la variété des procédés d’assemblage, celle des composants au sein de la chaîne d’approvisionnement, la répétabilité du système de test et les erreurs de manipulation des opérateurs sont autant de causes de défaillance des dispositifs. Or, certains de ces défauts ne sont pas détectés pendant les tests de fabrication en raison de la couverture insuffisante du système utilisé. Les unités ayant réussi les tests de justesse peuvent être à l’origine de défaillances en cours d’utilisation en raison de leurs performances dégradées.
Pour rester compétitives, les entreprises cherchent souvent à optimiser leurs tests de fabrication en limitant au maximum le coût par test et le temps de test. De ce fait, il arrive que certains dispositifs soient testés "au rabais".
À titre d’exemple, un fabricant de DM sans fil a récemment rencontré des problèmes d’efficacité avec son installation de test de production. La version personnalisée de son dispositif de communication BLE (Bluetooth Low Energy) avait franchi toutes les étapes de test pour finalement présenter des signes de connexion intermittente. Après dépannage, il s’est avéré que le diagramme d’antenne était déformé, provoquant une baisse significative de la puissance sur certains canaux BLE. Lors des tests de production, un unique - et très simple - test de connexion n’avait pas permis de détecter le problème.
Économiser en investissant
Remédier à un défaut identifié au cours des phases initiales de fabrication ne coûte généralement pas très cher. En revanche, ces dépenses augmentent de façon exponentielle lorsque la détection a lieu après les tests de production, ou in situ lorsque l’appareil est déjà en cours d'utilisation.
Il est primordial d’investir dans la solution de test appropriée lorsqu'il s'agit de lancer un nouveau produit. Il est certes coûteux d'investir dans un testeur RF (radiofréquences) et de rémunérer les opérateurs qualifiés pour s'en servir, sans compter les dépenses annuelles de maintenance et d’étalonnage. Mais la possibilité de détecter des défaillances de façon précoce, pendant la fabrication, permet d’éviter les coûts directs, indirects ou cachés d’une panne survenant sur le terrain. Les coûts cachés liés aux conditions de garantie, au dépannage, à la gestion des unités de remplacement, au manque à gagner induit par les atteintes à l’image de marque, voire aux pénalités inhérentes à l’utilisation de produits défectueux, peuvent effectivement atteindre des montants considérables.
En appliquant les stratégies de test appropriées en phase de production, les fabricants rentabiliseront facilement l’achat d’un testeur RF dès la première année. Le tableau ci-dessous présente un exemple des économies potentielles. Elles peuvent atteindre 250 000 $, notamment au niveau de la garantie, des coûts indirects/cachés en cas de rappel des produits, etc.
Dans la section suivante, nous allons voir comment certains fabricants de dispositifs médicaux optimisent les tests de fabrication pour garantir la qualité de leurs produits, augmenter leur rendement en fabrication, améliorer la flexibilité du système de test ou accroître le débit de fabrication.
Étude de cas n° 1 : assurer la qualité d’un chargeur communiquant en BLE
Un fabricant souhaitait pour la première fois intégrer une fonction de connectivité sans fil dans ses DM, à savoir un chargeur de batterie communiquant en BLE. Le but était de permettre aux utilisateurs de surveiller facilement l’état de charge et le niveau de la batterie afin d’en prolonger la durée de vie. Pendant la phase de conception, l’ingénieur a dû vérifier que l’antenne et les circuits d’adaptation fonctionnaient conformément aux objectifs. Le produit étant développé à l’aide d’un module RF, il a pu éviter les tests paramétriques, conformément aux spécifications Bluetooth. Les performances RF étaient en effet garanties par le fabricant du module. Ceci dit, ayant apporté des modifications à la conception de référence et à l’antenne dans le but de répondre aux exigences de format, l’ingénieur a dû procéder à une validation complète au niveau de l’appareil final afin de s’assurer que ce dernier transmettait et recevait les signaux BLE correctement dans différents scénarios d’utilisation.
L'entreprise a utilisé un testeur sans fil par voie aérienne (OTA pour Over the Air) spécialement conçu pour les applications connectées à l’IoT pour mesurer la puissance de sortie de l’émetteur, ainsi que le taux d’erreur par paquet (PER pour Packet Error Rate) et la sensibilité du récepteur. L’ingénieur s’est appuyé sur les mesures OTA pour valider les performances globales en émission et en réception, y compris au niveau de l’antenne. En outre, il pouvait soit tester la totalité des 40 canaux de fréquence BLE, soit sélectionner les canaux qui l’intéressaient. Cette option lui a permis de valider les performances de la radio dans l’ensemble de la bande de fréquences BLE.
L'entreprise utilise la même configuration de test au niveau de la production en raison de son faible coût et de sa simplicité d’emploi. Le test est optimisé en testant la puissance en émission (TX) et le PER en réception (RX) sur seulement trois canaux - fréquence inférieure, moyenne et supérieure - dans l’optique de valider rapidement les performances du dispositif dans l’ensemble de la bande de fréquence BLE. Le fabricant a ainsi pu accélérer la production de ses DM. Cela lui a aussi permis de minimiser les problèmes de corrélation rencontrés fréquemment en raison de la multiplicité des configurations de test utilisées lors des phases de conception et de fabrication.
Dans le cas de cette application, l'entreprise a économisé plusieurs semaines de développement de tests pendant la phase pilote, réduit ses délais de mise sur le marché et validé la qualité du produit en adoptant une méthode efficace couvrant l’ensemble des tests requis.
Étude de cas n° 2 : améliorer le rendement de production d’un DM à commande sans fil
Un autre fabricant a rencontré des problèmes de rendement sur la production de l’un de ses équipements chirurgicaux haut de gamme qui intègre un sous-système de commande à distance sans fil. Ce sous-système fonctionnait correctement jusqu’à ce que des défaillances fassent leur apparition. Ce problème a eu des conséquences significatives sur les livraisons, dans la mesure où les défaillances ont été découvertes une fois la machine entièrement fabriquée et testée. Lorsque le sous-système est tombé en panne, il a fallu beaucoup de temps pour le dépanner, le réparer et procéder à de nouveaux tests. Ce qui a provoqué l’accumulation des dispositifs non livrés, ainsi que des erreurs d’expédition.
Pour résoudre ce problème, le fabricant a décidé d’utiliser un testeur de signalisation IoT, simple et peu coûteux, afin de pré-tester les modules sans fil avant leur montage dans le sous-système de commande sans fil. L’identification des modules défectueux en amont de leur installation a permis au fabricant non seulement de gagner beaucoup de temps au niveau des tests ou des réparations, mais également d’atteindre ses objectifs de production et de rendement quotidiens.
Étude de cas n° 3 : accroître la flexibilité de production de wearables
Un sous-traitant spécialisé dans la fabrication de wearables à usage médical utilisait une solution de test monobloc ne pouvant opérer qu'en mode "sans signalisation". Un micrologiciel dédié devait être chargé sur l’appareil avant de lancer le test. Ce firmware était ensuite effacé et, une fois le test terminé, remplacé par le micrologiciel de production final.
La gestion de plusieurs jeux de micrologiciels pour différents produits constituait une tâche particulièrement fastidieuse pour l’équipe de fabrication. En outre, les erreurs de manipulation constituaient un risque majeur pour les opérateurs amenés à fabriquer un large éventail d’appareils pour différents clients.
Soucieuse d’améliorer la flexibilité de la production, ainsi que d’éliminer les erreurs de manipulation des opérateurs, la société a opté pour un testeur sans fil IoT capable d’exécuter des tests de signalisation par voie aérienne en utilisant le micrologiciel de production final. Cette solution lui a permis de rationaliser les processus de test, ainsi que de "basculer" sans difficulté entre différentes marques ou versions d’un produit. Le testeur utilisé prend également en charge les principaux protocoles de communications sans fil courte portée (BLE 4.2, BLE 5 et WLAN à 2,4 ou 5 GHz), ce qui permet de réutiliser la même configuration pour tester des appareils avec différents formats radio. Cette flexibilité permet aux fabricants à façon de répondre sans difficulté aux fluctuations de volume de leurs clients.
Étude de cas n° 4 : augmenter les cadences de fabrication et réduire le coût de test de wearables
Un fabricant de wearables souhaitait se doter d’une plateforme de test de nouvelle génération pour augmenter les cadences et réduire le coût par test sans en sacrifier la couverture, sachant que l’industrie médicale est intransigeante sur le plan de la qualité. Fastidieuse, la solution de test existante nécessitait une intervention soutenue de la part de l’opérateur. Elle impliquait en outre de placer manuellement l’appareil sous test (DUT) dans le boîtier blindé, d’exécuter le test, de retirer le DUT à l’issue du test, d’insérer un nouvel appareil à tester et de répéter le processus.
Cette solution qui fonctionnait en mode séquentiel a été remplacée par un outil capable de tester plusieurs appareils en parallèle avec, à la clé, une réduction significative des délais de test. L’opérateur peut en effet placer quatre dispositifs en même temps dans le boîtier blindé et procéder simultanément aux tests en émission (TX) et réception (RX) sur les quatre produits. À la fin des tests, l’opérateur retire les quatre DUT et les remplace par les quatre suivants. En se dotant ainsi de capacités de test en parallèle, le fabricant a réussi à diviser par plus de quatre la durée des tests tout en augmentant considérablement les cadences et en réduisant ses coûts.
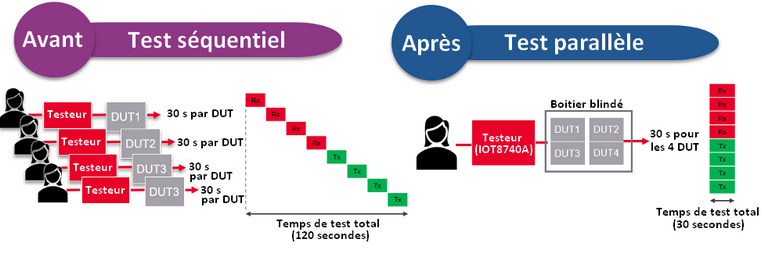
L’utilisation d’une solution de test OTA en parallèle, telle que la solution sans fil IOT8740A de Keysight, permet d’accélérer sensiblement les campagnes de test.
Conclusion
Les dispositifs médicaux connectés enregistrent une croissance exponentielle. L’ajout d’une connectivité sans fil apporte d’énormes avantages aux patients tout en améliorant et en réduisant le coût des prestations de santé. Le succès de cette tendance majeure dépend de la capacité des fabricants à commercialiser des dispositifs connectés fiables, de haute qualité, qui ne connaîtront pas de défaillances prématurées en conditions de fonctionnement normales. L’efficacité des tests de fabrication est essentielle pour garantir la qualité des produits en interceptant les unités défectueuses ou ayant réussi les tests de justesse, mais qui risquent de provoquer une défaillance une fois en service. Le choix d’une stratégie de test efficiente permet de minimiser ce risque sans accroître les coûts de fabrication.
[Source des illustrations : Keysight Technologies]