Comment tester la stabilité de son dispositif médical ?
Il incombe au fabricant d'un dispositif médical de garantir la stabilité de son produit durant l'ensemble de son cycle de vie. Le CEO d'Albhades, Michel Butin, expose ici l'environnement règlementaire de référence et la théorie sur laquelle se baser pour tester cette stabilité. Fort de sa solide expérience dans ce domaine, il propose une stratégie à adopter.
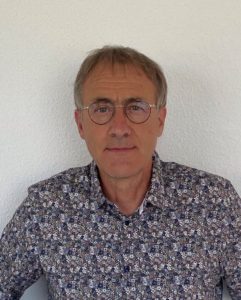
"On dispose rarement de marqueurs précis de dégradation et le choix des conditions de température et d'humidité est généralement empirique" - Michel Butin (source : Albhades)
Par Michel Butin, CEO du groupe Albhades
Au cours de sa vie, le dispositif médical (DM) est exposé à des influences extérieures pouvant modifier ses qualités physico-chimiques et/ou son intégrité. Le fabricant devra donc s'assurer de la maîtrise de ces phénomènes tout au long de la vie du dispositif en conditions réelles de conservation et, s’il souhaite obtenir des résultats plus rapidement, en conditions maximalisantes.
Quel est le contexte règlementaire ?
Les DM sont soumis aux dispositions du règlement (UE) N° 2017/745 du Parlement européen et du Conseil (RDM) qui précise à l’Annexe II / chapitre 6 : « La documentation contient les résultats et les analyses critiques de l'ensemble des études et/ou des essais de vérification et de validation qui ont été effectués pour démontrer que le dispositif respecte les exigences du présent règlement, en particulier la stabilité, y compris la durée de conservation en stock ».
Si le RDM prévoit l’exigence, il ne décrit pas les moyens pour s’y conformer. Il faut donc rechercher ailleurs une méthode pour y parvenir.
Les BPF (ISO 13485) ou les cGMP (FDA 21CFR part 820), tout comme le RDM, imposent de maîtriser la stabilité du packaging durant le stockage. Néanmoins, là encore, aucune méthode d’évaluation de la durée de vie n’est prévue.
Il existe une norme spécifique à la stabilité des DM destinés aux réactifs de diagnostic (ISO 23640) mais elle n’apporte aucune information sur les paramètres à appliquer.
Il existe toutefois une norme américaine qui peut servir de guide pour le fabricant de DM : l’ASTM F1980:2021. Cette norme traite spécifiquement de l’accélération par la température et l’humidité forcées de la dégradation de la barrière stérile du DM. Néanmoins, elle prévoit dans son objet de l’élargir à d’autres paramètres. Les principes généraux permettant de justifier le temps et les paramètres d’essai au regard de la durée de vie revendiquée ont le mérite d’y être clairement expliqués.
Température : les préconisations de l'ASTM F1980:2021
De manière générale, le principal facteur d'accélération est la température à laquelle va être conduit l’essai. Plus on chauffe, plus on raccourcit le temps d'incubation au regard du temps de vie revendiqué. Toutefois, plus on s'éloigne des conditions standard et plus le système diverge du modèle théorique. A des températures élevées, des phénomènes nouveaux qui ne se produiront pas à température ambiante peuvent alors apparaître (effet de seuil).
C’est donc une analyse de risque et l’expérience du fabricant qui permettront de trouver le meilleur compromis entre la durée de l'étude et la température maximale acceptable par le produit. Il faut noter que l’ASTM F1980:2021 précise : « Temperatures higher than 60°C are not recommended ».
Une lecture conservatrice de cette recommandation tenant compte du fait que la régulation de température doit être comprise dans un intervalle de +/– 2°C peut conduire à recommander plutôt un maximum de 58°C.
La loi d’Arrhenius prévoit une relation entre la vitesse de réaction (k) la température (T), l’énergie d’activation propre à cette réaction (Ea) :
Ln k = 10*Q10– Ea/(RT)
R étant la constante universelle des gaz parfaits
Q10 correspond au facteur d’accélération induit par une élévation de 10°K. Il est propre à chaque réaction. Les valeurs de Q10 généralement rencontrées vont de 1,8 à 3,3.
Pour une température de stockage envisagée (Ts), on peut calculer à partir de la loi d’Arrhenius, une réduction du temps d'essai (Te) associée à une augmentation de la température (ϴe-ϴs) en choisissant un Q10 suffisamment conservateur mais assez élevé pour que la réduction du temps soit significative.
L’ASTM F1980:2021 propose l’équation suivante avec une valeur de Q10 par défaut de 2 :
Te = Ts / 2((ϴe-ϴs)/10)
Il convient néanmoins dans le dossier de justifier ce choix (en général en écrivant que l’analyse de risque ou l’expérience ne conduit pas à envisager une réaction de dégradation plus lente…).
Humidité : tenir compte des "absorbants"
L’humidité relative dans une enceinte (HR) est le rapport exprimé en pourcentage entre la pression partielle en eau et la pression de vapeur saturante (PVS). De ce fait, pour une même quantité d’eau, si la température augmente alors la PVS augmente et l’HR diminue. La stabilité d’une poudre ou d’une colle de packaging est intimement liée à l’activité de l’eau (aW), qui elle-même est en équilibre avec l’HR de l’environnement.
Comme dans le modèle « température », le taux de dégradation (k), est directement lié à l’HR par l’équation :
Ln k = B(HR) + C
B et C étant des constantes
B peut varier, selon les types de dégradation, de 0 à 0,09, ce qui induit des accélérations très significatives liées à l’augmentation d’HR. Pour un passage de 20% à 80%, la réaction peut être accélérée jusqu’à 220 fois !
On devrait donc déduire qu’une étude de stabilité accélérée doit se faire à HR au minimum constante voire augmentée. En pratique, les produits contiennent souvent des « absorbants » qui, lorsqu’on ajoute de l’eau pour maintenir l’HR à température plus élevée, se saturent beaucoup plus vite. L’excédent d’humidité vient alors impacter directement le produit alors qu’il ne l’aurait pas fait à température ambiante. Il est donc conseillé de mener des essais en maintenant simplement l’HR moyenne revendiquée.
Stratégie proposée
On a rarement des marqueurs précis de dégradation et l’approche est généralement empirique. Le choix de la température s’effectuera en fonction de l’analyse de risque en faisant malgré tout en sorte de ne pas s’éloigner déraisonnablement des conditions de conservation. Une fois la température choisie, on peut calculer à l’aide de la fonction dérivée de la loi d’Arrhenius le temps d’essai en appliquant un Q10 conservateur de 2.
Concernant le choix des conditions d’humidité, il est recommandé de conserver une humidité relative équivalente à l’humidité relative atmosphérique. L’ASTM F1980 recommande de rester dans une plage 45-55 % HR qui est l’humidité relative moyenne à 25°C en zone tempérée et, en tout état de cause, de ne pas dépasser 55% HR au risque d’induire de nouvelles dégradations.
INFO
Albhades se distingue par sa combinaison d'expertises en toxicologie, physico-chimie, microbiologie et biologie cellulaire. Ces expertises permettent un accompagnement personnalisé dans le cadre des validations de procédés et de biocompatibilité. L'entreprise sera présente à Médi'Nov sur le stand 88.
Pour un dispositif médical pour lequel on n’a pas de donnée précise sur la cinétique de dégradation et pour lequel on souhaite recommander une conservation de 60 mois à 25°C à 45-55% d’humidité, nous préconisons donc les conditions suivantes :
- si le produit supporte 60°C sans apparition de phénomène critique : 58 ± 2°C et 50 ± 5 % HR pendant 185 jours ;
- si le produit doit être incubé à plus basse température (rare pour les DM), alors la loi d’Arrhenius vous permettra de calculer le temps d’incubation.