Impression 3D : un vecteur de compétitivité dans le dispositif médical
Du test sur modèles anatomiques jusqu'à la production de pièces d'usage final, en passant par la réalisation d'outillages spécifiques, l'impression 3D de dernière génération offre de nombreuses possibilités aux fabricants de dispositifs médicaux en quête de compétitivité.
L'impression 3D a évolué de façon importante et permet aux fabricants de dispositifs médicaux d'être bien mieux armés pour répondre aux défis majeurs de réduction des coûts et d’accélération de la mise sur le marché. Le tout dans le respect de normes de qualité strictes et le maintien d'un niveau élevé de précision. Avec les nouvelles technologies de pointe, le secteur des technologies médicales se voit en effet offrir des moyens concrets d’optimiser l’ensemble de ses process de production.
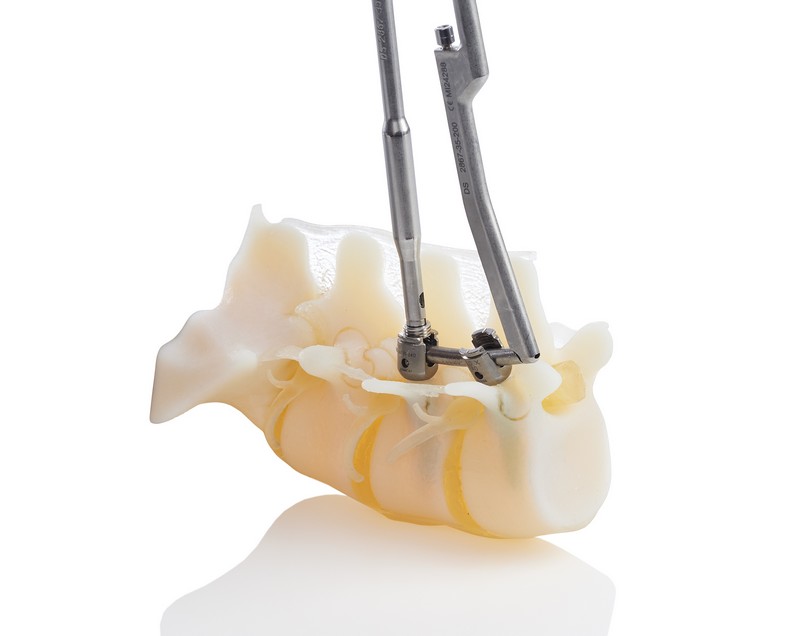
Vis pédiculaire insérée dans un modèle imprimé en 3D de la colonne vertébrale d’un patient (crédit photo : Stratasys).
Des modèles anatomiques réalistes pour des tests plus efficaces
La technologie PolyJet de Stratasys est particulièrement adaptée à la création de modèles anatomiques hyper-réalistes, à partir de matériaux comme le GelMatrix, le BoneMatrix, le TissueMatrix et le RadioMatrix. Ceux-ci reproduisent fidèlement les tissus humains et les os, en répliquant leurs comportements, leur niveau de souplesse et de rigidité, jusqu’à leur radio-opacité.
De nombreux CHUs comme celui de Brest et l'AP-HP utilisent déjà ces modèles pour la formation et la planification chirurgicale, mais cette technologie est tout aussi pertinente pour les fabricants de dispositifs médicaux souhaitant améliorer leurs phases de tests précliniques.
En effet, la validation de nouveaux produits nécessite souvent des tests coûteux et complexes sur des cadavres ou des animaux, retardant ainsi les phases de validation. Avec l'impression 3D, cette étape critique peut être repensée. Les tests sur des modèles anatomiques réalistes permettent aux fabricants d’optimiser les performances cliniques des nouveaux dispositifs, avant de les soumettre aux autorités de régulation. Grâce aux multiples itérations possibles avec cette technologie, il leur est désormais possible d’anticiper les défauts et ainsi d’accélérer la mise sur le marché tout en réduisant les coûts.
Stratasys propose également des matériaux biocompatibles comme le Clear MED610 ou le Digital ABS Plus, qui permettent de réaliser des tests directement sur la peau humaine. Cela ouvre la voie à des essais plus sûrs et plus rapides, tout en respectant les exigences réglementaires strictes de la FDA ou de l’EMA.
Amélioration de la production : de l'outillage aux pièces finales
Autrefois limitée au prototypage, l’impression 3D rivalise aujourd'hui avec les méthodes de production conventionnelles, notamment en termes de précision, de répétabilité et de conformité réglementaire. Elle offre des avantages considérables pour la fabrication de gabarits, posages et outillages spécifiques, mais aussi de pièces d’usage final de petite et moyenne série.
Un webinaire le 28 novembre 2024
Pour creuser le sujet, Stratasys et Cylaos organisent, le 28 novembre prochain, un webinaire intitulé "Innovation en Santé : L'impact de l'impression 3D sur la fabrication des dispositifs médicaux".
Pour s'inscrire, cliquer ici.
Là où les méthodes traditionnelles montrent leurs limites en termes de liberté de conception, de coûts et de délais de production, la fabrication additive peut être une excellente alternative avec des matériaux répondant aux cahiers des charges les plus exigeants : résistance aux très hautes températures, résistance à l’étirement, réduction de poids des pièces, caractéristiques antistatiques...
Parmi ces matériaux, l'ULTEM 1010, aux propriétés biocompatibles, permet de fabriquer des outils personnalisés, robustes, même dans des environnements aux exigences strictes tel que le pharmaceutique. Des entreprises comme Medtronic et les laboratoires pharmaceutiques UPSA utilisent déjà ces solutions pour développer leurs outillages, faire de l’amélioration continue sur leurs machines spéciales et accélérer les cycles de production.
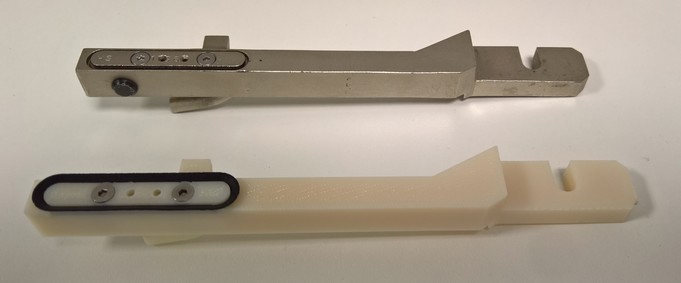
Supports de caméra imprimés en 3D pour les besoins d'une ligne de production chez UPSA (crédit photo : Stratasys).
Autre exemple, le fabricant spécialisé dans les produits d’administration de médicaments Presspart a réduit de 50 % ses coûts d’outillage en recourant à la technologie DLP P3 au lieu du moulage par injection pour la production de ses inhalateurs. Ses délais de fabrication sont passés de plusieurs semaines à 24 h, tout en maintenant une précision de 50 µm.
Au-delà de l'outillage, les technologies de poudre SAF et de résine DLP P3 permettent de produire des pièces d’usage final, avec un excellent état de surface et des propriétés mécaniques adaptées. On obtient ainsi des petites à moyennes séries de pièces finales avec une précision et une stabilité dimensionnelle quasi similaires à celles qu’offre le moulage par injection, mais à moindre coût. C’est le cas de Go Orthotics, qui fabrique des orthèses sur mesure, directement imprimées en 3D.