Equipements de production > Logiciels
Est-il pertinent de programmer ses machines-outils avec le logiciel Esprit ?
Tout dépend bien sûr des cas de figure, mais il est intéressant de considérer le retour d'expérience du site français de Stryker Spine. Neuf ans après avoir investi dans le logiciel de programmation globale Esprit, son équipe explique les avantages qu'elle en a tirés et comment elle compte enfoncer le clou avec le système expert "Knowledge Base Machining".
A l’origine, l’américain Dr Homer Stryker invente un lit à retournement pour faciliter les opérations, qui sera beaucoup utilisé pendant la seconde guerre mondiale. Avec 25 000 employés, le groupe fabrique aujourd'hui un large éventail de dispositifs médicaux, notamment sur son site de production français à Cestas.
Les ateliers bordelais utilisent des centres de tournage robotisés et les derniers modèles de machines-outils comme les Mazak Integrex ou Variaxis, la DMU de DMG, la TNL, des modèles Stama, Star, ou Iemca. Ces machines permettent de fabriquer principalement des plaques pour rachis cervical et lombaire en titane, des cages ou des crochets en PEEK, ainsi que des instruments et des vis à os. Le savoir-faire du fabricant repose donc sur la précision, la maîtrise des formes gauches et des matières difficiles à usiner.
En 2006, la fabrication assistée par ordinateur (FAO) n'était pas vraiment nécessaire car les opérations et les pièces étaient encore simples. Mais conscients de l’évolution industrielle, les responsables du site décident à l'époque d’investir dans un logiciel de programmation global permettant d’assurer plus facilement toutes les opérations de décolletage, de fraisage, de tournage et d'électro-érosion. Leur choix se porte alors sur le logiciel de FAO Esprit de DP Technology, utilisé depuis 1997 au siège chez Stryker Instruments USA et dans la filiale chinoise.
Augmenter à la fois la productivité et la complexité des pièces
Après la mise en place de la FAO, en collaboration avec la R&D et le Service Qualité, la production des ateliers a évolué vers l’usinage en 5 axes continus et les formes libres. Ce qui a permis de réaliser des pièces très complexes et des instruments de haute-précision, avec la possibilité de repenser le design. C'est en fait une nouvelle philosophie d’usinage qui a pris forme, comme l'explique Franck Duru, aujourd’hui Technicien Méthodes et Spécialiste FAO : "Nous nous efforçons de programmer rapidement en réutilisant toujours des cycles existants ; mais aussi de simplifier par familles de pièces, en pensant à toutes les autres qui vont arriver ensuite. Car parfois seules les dimensions varient."
Avec les 13 licences du logiciel, l’équipe des techniciens programment toutes les machines. Ils utilisent principalement les modules 3D, et aussi la reconnaissance de formes pour certains produits. Dans la structure suisse à La-Chaux-de-Fonds, spécialisée dans les implants orthopédiques, les machines sont pilotées avec des programmes réalisés à Cestas.
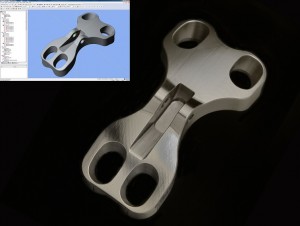
Plaque d’implant lombaire usinée en 5 axes avec le logiciel Esprit. Temps de programmation : une journée.
Franc Duru prend l'exemple d'une plaque pour implant lombaire : « Rien n’est plat sur ce genre de pièce, et il faut la faire la plus fine possible pour être supportée par le patient. Pour mettre au point son usinage, il m’a fallu une journée de programmation. Mais sans les stratégies d'Esprit 2014, le travail aurait pris plusieurs semaines. »
L’usinage réalisé en 5 axes continus avec le logiciel de FAO comprend de nombreuses étapes : ébauche grande vitesse avec le nouveau cycle Profit Milling, fraisage composite pour un meilleur état de surface, contournage, taraudage, lamage… Nicolas Marsault, directeur d’Usiprog, partenaire intégrateur Esprit chez Stryker, explique que « La technologie du Profit Milling a permis d’usiner le brut en poche ouverte et le contour de la pièce en îlot. Ce qui représente un gain de temps et une économie d’outil. »
Stryker réalise dans leur totalité des pièces chirurgicales en PEEK, comme des cages placées entre les vertèbres avant de fixer les plaques, ou des crochets pour bloquer les tendons. Les détails sont minuscules et la matière compliquée à usiner, à cause du risque de bavure. "Les produits sortent des cellules robotisées en une journée alors qu’avant cette robotisation, il fallait 8 jours, » souligne l’opérateur Cédric Lassus Debat. « Les pièces sortent finies, sablées, gravées, et prêtes à être expédiées. On usine sur un tour Realmeca et on insère le marqueur en titane avec Esprit. Un robot récupère la pièce et la grave, puis la déplace dans une cellule de sablage.»
Une ouverture d'Esprit pour optimiser la programmation
A l’origine, le design de chaque pièce est réalisé avec le logiciel de conception assistée par ordinateur (CAO) de PTC. Grâce à l’outil d’échange de données Esprit Feature Exchange, le logiciel de FAO récupère toute l’arborescence de la CAO avec tous les détails de la pièce. On parle d’associativité. Cela permet une transmission des données fluide et une programmation plus précise.
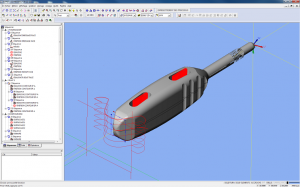
Instrument usiné sur une machine multitâches Stama 726MT, permettant de contrôler la taille du Spacer (cage) à implanter entre deux vertèbres.
La disponibilité d’outils de développement en VBA au sein du logiciel permet davantage d’automatisation et de sécurité. Par exemple, grâce au développement d’un add-in spécifique, les données d’outils sont récupérées dans l’interface et un clic suffit pour publier un rapport d’outillage pour l’atelier. « Avant on les entrait à la main. Pour des pièces qui demandaient 20 outils, il fallait 1 heure ou 2. On gagne 90% du temps car on évite la vérification et les erreurs, » détaille le spécialiste FAO.
La coopération de l’éditeur du logiciel avec les constructeurs de machines permet de fournir des licences adaptées aux machines et des post-processeurs certifiés. Franck Duru précise que « Les post-processeurs fournis par Usiprog sont productifs dès leur installation. Le gain de temps est supérieur à 30%. Grâce aux post-processeurs standard de DP Technology, les programmeurs n’ont en effet pas besoin de les développer de A à Z. Même en cas de modification de programmation pour une nouvelle pièce, le risque d’erreur est quasi-nul» .
Un système expert pour capitaliser le savoir-faire
La renommée et la croissance à 2 chiffres de Stryker doivent beaucoup aux efforts d'investissements que le groupe maintient chaque année. Dans la filiale bordelaise, le Chef d’atelier Janick Sabria reste confidentiel sur les projets à venir mais confie qu’il est prévu d’acheter de nouvelles cellules robotisées et des machines de palpage.
Côté logiciel, l'équipe prévoit une nouvelle étape d'investissement, avec l'option Knowledge Base Machining du logiciel Esprit. Celle-ci fournit une approche presse-bouton qui permettra à ses utilisateurs de déterminer la meilleure méthode pour usiner une pièce ou une séquence donnée. Il suffira de sélectionner automatiquement les outils de coupe, les paramètres d’usinage et les cycles les mieux adaptés. Il s'agit tout bonnement d'un système expert de production, adossé à une base de données Multi-Utilisateur SQL Serveur, dont le but est de capitaliser le savoir-faire et d’accroitre la productivité.
DP Technology, F-34000 Montpellier, www.dptechnology.com