Quand l’impression 3D sert aussi le besoin de conditionnement des DM
Le fabricant d’implants orthodontiques Tita-Link cherchait à améliorer le conditionnement de ses vis jusque-là livrées en sachets. Il a trouvé la solution en sous-traitant la fabrication additive de conteneurs à usage unique auprès de Steriservices, qui utilise une imprimante signée 3D Systems.
La fabrication additive permet aux fabricants de dispositifs médicaux (DM) de mettre au point des produits innovants de manière rapide et rentable, mais aussi de s'adapter efficacement à la demande.
Au delà des applications de prototypage, devenues classiques, la fabrication additive est utilisée pour produire des outils chirurgicaux spécifiques au patient à partir des données d'imagerie, ou encore des implants et des instruments présentant des caractéristiques impossibles à obtenir par la méthode soustractive traditionnelle.
Mais l'impression 3D répond également à certaines problématiques de conditionnement de DM. Tita-Link peut en témoigner.
Basé à Bruxelles, ce fabricant de dispositifs médicaux est spécialisé dans les implants destinés à des applications maxillo-faciales et orthodontiques, y compris les vis minuscules pour la chirurgie buccale.
Un boitier au lieu d'un sachet
Traditionnellement, ces vis étaient emballées dans des sachets : une solution qui rendait leur manipulation délicate pendant l'opération et qui n'était pas satisfaisante sur le plan environnemental. Les vis devaient être placées dans des plateaux spécifiques par l'infirmière avant l'opération, ce qui entraînait une perte de temps et un risque accru de contamination.
A la recherche d'une option de conditionnement plus viable, Tita-Link a déterminé que la meilleure solution serait d'utiliser des conteneurs sous la forme de boîtiers personnalisés à usage unique qui pourraient être produits rapidement et à faible coût. En raison des quantités limitées et des délais très courts dans lesquels ils devaient être fabriqués, le moulage par injection n'était pas envisageable.
Le fabricant belge a donc décidé de produire les boîtiers par fabrication additive. Ne disposant pas d'installations d'impression 3D certifiées ISO 13485 en interne ni de processus validés, il a dû externaliser cette opération.
Steriservices : le partenaire idéal
Tanguy de Schoutheete, directeur technique de Tita-Link, a contacté Steriservices avec qui son entreprise entretient un partenariat de longue date.
Rappelons que Steriservices est spécialisé dans la stérilisation mais aussi dans le conditionnement à façon de dispositifs médicaux. Et il se trouve qu'en tant que partenaire technique, l'entreprise française disposait déjà d'un workflow certifié et validé pour les dispositifs médicaux. Elle a pu prendre en charge ce projet pour Tita-Link en complétant ses technologies de fabrication traditionnelles par la fabrication additive.
Sachant que de nombreuses technologies d'impression 3D pouvaient être utilisées, Tita-Link et Steriservices ont dû identifier celle qui se prêtait le mieux à la fabrication des boîtiers. Le choix s'est porté sur une solution proposée par 3D Systems, pionnier de la technologie d'impression 3D, dont l'équipe d'experts est passée maître dans la conception et la production de dispositifs médicaux.
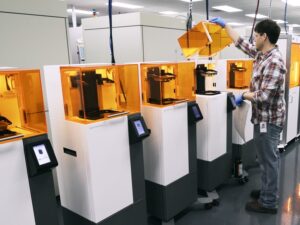
L'imprimante Figure 4 Stand-alone, qui utilise des matériaux biocompatibles et stérilisables, a été validée pour une utilisation dans les applications de santé (crédit photo : 3D Systems).
La Figure 4 Standalone utilisée avec un plastique stérilisable
Après analyse des besoins de Tita-Link, les ingénieurs en applications de 3D Systems ont conçu une solution associant l'imprimante Figure 4 Standalone avec le matériau Figure 4 Tough 60C White de l'entreprise.
L'imprimante se présente comme un matériel abordable et polyvalent, adapté à la production de petites séries et au prototypage "le jour même", pour permettre une itération et une vérification rapides de la conception. Elle permet d'obtenir des pièces dont la finition est similaire à celle des pièces produites par moulage par injection.
Quant au matériau, il est biocompatible (ISO 10993-5 et -10) et présente une résistance élevée aux chocs et à la traction, ainsi qu'un bon allongement. Il est donc adapté à la production en série de pièces médicales supportant des charges mécaniques élevées. Il est aussi stérilisable aux rayons gamma et à l'ETO, une nécessité pour pouvoir être introduit dans le bloc opératoire.
En collaboration avec Tita-Link et Steriservices, 3D Systems a contribué à la conception du boîtier et l'a optimisée pour l'impression à l'aide du logiciel 3D Sprint, fourni avec la machine Figure 4. L'intérêt de 3D Sprint est notamment de tirer parti de la fonction d'empilage unique de cette imprimante, pour une production rapide et efficace de pièces. Au final, Steriservices peut produire 105 boîtiers par jour, soit près de 23 000 par an.
A noter que Steriservices est désormais en mesure, si elle le souhaite, d'étendre l'utilisation de cette solution à d'autres dispositifs médicaux, y compris les instruments jetables, et d'élargir ainsi la gamme de produits proposés à ses clients.
A voir sur le stand P07, Hall 8b, de Compamed 2023