Solutions de connexion surmoulées au silicone et livrées pré-qualifiées
Acteur d'envergure mondiale sur le marché du connecteur, ODU consacre 30 % de son activité au marché des dispositifs médicaux. Le groupe propose notamment le surmoulage silicone d'assemblages complets connecteur/câble et réalise toute la batterie de tests exigés par la réglementation.
Par Evelyne Gisselbrecht
Le groupe ODU en bref
Présent dans le monde entier
ODU fait partie des principaux fournisseurs internationaux de solutions de connexion et emploie 2700 personnes dans le monde, dont 1500 à son siège social de Mühldorf am Inn en Bavière. Le site allemand a été dupliqué à Sibiu en Roumanie mais le groupe compte aussi des centres de production et de développement de produits à Shanghai (Chine), à Tijuana (Mexique) et à Camarillo (USA). ODU possède ses propres filiales de distribution, notamment en France, mais aussi dans de nombreux pays d'Europe et d'Asie ainsi qu'aux Etats-Unis. Le groupe, qui compte 6000 clients au monde, a réalisé en 2023 un chiffre d'affaires de 190 millions d'euros. Il prévoit la construction de deux nouveaux bâtiments à Mühldorf et celle d'un nouveau centre logistique est en cours. Les connecteurs d'ODU assurent une transmission fiable de la puissance, des signaux, des données et des protocoles haut débit dans de nombreux domaines d'application exigeants : la medtech, le militaire et la sécurité, l'automobile ainsi que l'électronique industrielle et le domaine de la mesure et du test.
L'histoire du groupe ODU remonte à plus de 80 ans mais c'est en 1955 que l'entreprise prend une nouvelle orientation, avec l'obtention d'un brevet pour son système de contact SPRINGTAC. Son inventeur Otto DUnkel a en effet une idée de génie : disposer à 360° des fils ressorts à la manière des brindilles de bois d'un balai. Il en résulte une grande résistance aux vibrations et une faible résistance de contact. Cette technologie de connexion est toujours utilisée aujourd'hui dans de nombreuses applications telles que les appareils d'IRM, les respirateurs ainsi que différents équipements de salles d'opération.
La gamme SPRINGTAC a été complétée depuis par de nombreux modèles de contacts et de connecteurs ODU : le groupe propose plus de 90.000 références et se distingue par la grande diversité de ses produits, qu'ils soient en métal ou en plastique, rectangulaires (par exemple la gamme ODU-MAC) ou circulaires. Au rang des connecteurs circulaires figure en particulier la gamme ODU MEDI-SNAP en plastique stérilisable, conçue spécifiquement pour le secteur médical.
Pour autant, les produits standards au catalogue d'ODU ne représentent pas la majeure partie de son chiffre d'affaires. L'entreprise consacre en effet plus de la moitié de son activité à la réalisation de solutions personnalisées selon le besoin des clients.
Une production intégrée à 80 %
La visite du site d'ODU à Mühldorf am Inn, à l'Est de Munich, est pour le moins impressionnante : 42.000 m² dédiés à la production, la fabrication étant réalisée à 80 % en interne. L'usine comprend notamment :
- un atelier de fabrication de moules et d'outillages ;
- un atelier d'injection plastique pour la fabrication des inserts qui viendront isoler les contacts électriques et pour les corps de connecteurs en plastique, par exemple ceux de la gamme ODU MEDI-SNAP. Ces connecteurs se caractérisent par leur taille compacte, leur faible poids, mais aussi leur haute densité de contacts. Ils sont utilisés en particulier pour des applications d'endoscopie, d'arthroscopie ou pour des capteurs de suivi de patients ;
- un atelier de décolletage équipé de plus de 160 tours pour la fabrication des contacts dans une large gamme de matériaux et de diamètres (de 0,5 à plus de 80 mm) ainsi que celle des corps métalliques ;
- un atelier de découpe pour la production de contacts en gros volume ;
- un atelier de traitement de surface, les contacts et les corps de connecteurs pouvant être galvanisés en bandes - avec possibilité d'un traitement sélectif - ou individuellement en grappes avec contrôle optique manuel ;
- un atelier d'assemblage, par exemple pour l'intégration des contacts dans les inserts. Les opérations sont manuelles ou 100 % automatisées selon les cas. En effet, ODU conçoit aussi ses propres machines spéciales pour certains assemblages.
Ce fort taux d'intégration de la production permet aux clients de bénéficier d'un interlocuteur unique qualifié et de délais de livraison mieux maîtrisés.
Surmoulage silicone : une opération délicate
ODU ne se limite pas à la fabrication de connecteurs, aussi complexe soit-elle. Le groupe fournit le plus souvent à ses clients un ensemble connecteur/câble assemblé, en réponse à leur besoin spécifique.
Pour le secteur des technologies médicales, qui représente 30 % de son activité, et plus particulièrement pour les applications impliquant des agressions mécaniques ou chimiques, l'entreprise est en mesure de réaliser un surmoulage silicone sur ces assemblages. C'est par exemple le cas pour les solutions intégrant un connecteur ODU MINI-SNAP série K.
Les câbles sont fournis à ODU par des fabricants rompus aux spécificités du secteur médical avec lesquels ODU travaille en étroit partenariat depuis de longues années. Ces fabricants lui garantissent, contrat à l'appui, l'utilisation d'un matériau bien défini pour l'enveloppe du câble, de manière à obtenir toujours la même qualité d'adhérence du silicone.
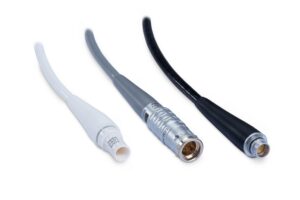
De g. à d. : connecteur ODU MEDI-SNAP, en plastique stérilisable, connecteur en métal ODU MINI-SNAP, et connecteur ODU AMC HIGH-DENSITY avec verrouillage à vis ou largable (crédit photo : www.berg12.de Michael Namberger).
Les solutions surmoulées d'ODU présentent de nombreux avantages :
- elles ne collent pas, ce qui les rend plus agréables au toucher mais surtout plus hygiéniques ; elles ne vous glissent pas entre les doigts ;
- elles supportent jusqu'à 500 cycles d'autoclavage ;
- elles offrent une excellente résistance à la torsion ;
- elles se prêtent à un marquage laser personnalisé, qu'il s'agisse d'un code barre, d'un logo, d'un numéro de série... ;
- elles sont exemptes d'halogène et de latex ;
- elles sont faciles à nettoyer ;
- elles peuvent être désinfectées par essuyage.
Des ensembles livrés pré-qualifiés
Mais ODU ne s'arrête pas là. L'entreprise effectue également en interne tous les tests nécessaires aux validations demandées par la réglementation propre aux dispositifs électro-médicaux :
- tests de résistance à l'autoclavage,
- tests de résistance aux environnements difficiles (brouillard salin, fortes températures, froid),
- essais d'étanchéité,
- tests d'adhérence,
- essais de biocompatibilité selon la norme ISO 10993-5 (cytotoxicité).
Le client reçoit ainsi un produit plug and play pré-qualifié.
ODU prélève les eaux de l'Inn pour refroidir ses machines et récupère la chaleur générée pour chauffer ses bureaux. L'eau est ensuite rejetée dans l'Inn à température contrôlée. Autre démarche écologique, l'entreprise trie tous ses déchets, les nettoie et les réinjecte si possible dans la production.
Cette technologie est adaptée aux gammes standard de connecteurs d'ODU et aux solutions sur mesure. Elle répond aux attentes du secteur de l'endoscopie, de la robotique chirurgicale, du monitoring ainsi que du secteur dentaire.
Toute l'attention focalisée sur le besoin du client
Pour ODU, il est essentiel de bien cerner la demande du client dès le départ. Ses ingénieurs commerciaux ont toutes les compétences techniques nécessaires pour obtenir les précisions requises. La demande du client est ensuite analysée par le centre d'applications de Mühldorf qui étudie le projet, liste l'ensemble de ses exigences techniques et économiques et recense les multiples possibilités existantes dans l'entreprise. Il décide alors si le projet nécessite un développement spécifique, puis un cahier des charges est défini avec le client, en collaboration avec la production et le département qualité. Le client bénéficie ainsi de toute l'expertise cumulée du groupe et de sa longue expérience.