IML : pour des DM étiquetés « dans la masse »
Désormais courante dans l’industrie de l’emballage agro-alimentaire, l'IML pourrait bien s'imposer dans certaines applications médicales. Arburg montre la voie dans ce domaine avec une solution développée en partenariat, qui répond aux besoins de l'étiquetage de tubes.
Le procédé In-Mould-Labelling (IML) ou "étiquetage dans le moule" consiste à intégrer directement une étiquette pré-imprimée (généralement en polypropylène) à la surface d'une pièce de même nature au moment du moulage par injection.
L'Allemand Arburg avait fait la démonstration, pour la première fois au salon Fakuma 2023, d'une solution IML dédiée au secteur médical, développée avec plusieurs partenaires : Kebo (moules), MCC/Verstraete (étiquette), Beck Automation (automatisation) et Intravis (contrôle par caméra). Il s'agit d'un projet commun consistant à permettre de produire des tubes de centrifugation étiquetés de manière rapide et économique, sans risque de contamination, à l'aide d'une installation clé en main.
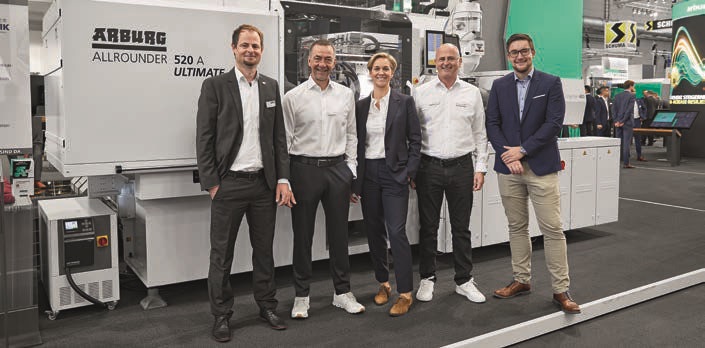
Fiers de cette application médicale innovante (de g. à d.) : Sven Kitzlinger (Arburg), Johannes Strassner (Kebo), Kim Blondeel (MCC Label), Ralf Ziemer (Beck Automation) et Malte Westermann (Intravis) (crédit photo : Arburg).
« Ensemble, nous avons développé un concept qui montre le potentiel que représente désormais le procédé IML pour les produits médicaux et pharmaceutiques », a déclaré Sven Kitzlinger, expert Medtech chez Arburg. « Nous voulons établir de nouvelles références en combinant nos savoir-faire », ajoute Johannes Strassner, directeur général de Kebo.
Un process plus durable
La technologie d’avenir présentée sous forme de "Preuve de concept" a rencontré depuis une forte résonance selon les informations qui nous ont été communiquées par Arburg. Le produit séduit en particulier en termes de durabilité : le tube et l’étiquette sont tous deux fabriqués en polypropylène (PP), ce qui permet de recycler facilement le produit monomatériau. L’étiquette intégrée pouvant contribuer à la stabilité du tube, il est possible, le cas échéant, de réduire l’épaisseur de paroi et donc la quantité de matière. Evidemment, l'IML élimine la nécessité de coller une étiquette ou d’imprimer à la surface du produit, ce qui évite l’utilisation d’adhésifs ou la contamination que peut représenter la peinture liquide.
Un autre atout que le fabricant allemand met en avant concerne la surface au sol de la cellule de fabrication qui a été développée. La machine choisie comme base de cette cellule est une presse électrique Allrounder 520 A Ultimate avec une force de fermeture de 1 500 kN. C'est un équipement qui a été conçu pour des processus rapides et exigeants, en salle blanche ISO 7. Avec un moule à 8 empreintes signé Kebo, des tubes prêts à l’emploi de 15 ml chacun sont fabriqués en un temps de cycle d’environ dix secondes.
Une cellule compacte d'une grande précision
Les étiquettes, dont l’épaisseur est de 57 µm, doivent être positionnées le plus précisément possible dans les empreintes. « Alors que la distance "Print to Cut" peut atteindre 1,5 mm pour les décorations IML destinées aux produits de conditionnement, elle n'est ici que de 0,2 mm », explique Kim Blondeel, Business Development Managerin chez MMC/Verstraete.
L’exactitude de l'alignement et de l’application des étiquettes est assuré par une automatisation réalisée par Beck Automation. « Notre tête d’ajustement des étiquettes peut compenser les tolérances de fabrication à quelques centièmes près », souligne Ralf Ziemer, Sales Manager Medical chez Beck. « C’est une condition importante pour la fonctionnalité, qui réduit de manière significative les variations de qualité et les rebuts. »
Intégré dans l’automatisation, le système de vision d'Intravis se charge de l'inspection visuelle des pièces finies en temps réel. Au delà du contrôle, le vissage des tubes et leur emballage dans des sachets tubulaires pourraient, dans une application réelle, être réalisés au sein de la cellule de fabrication.
Diverses fonctions possibles
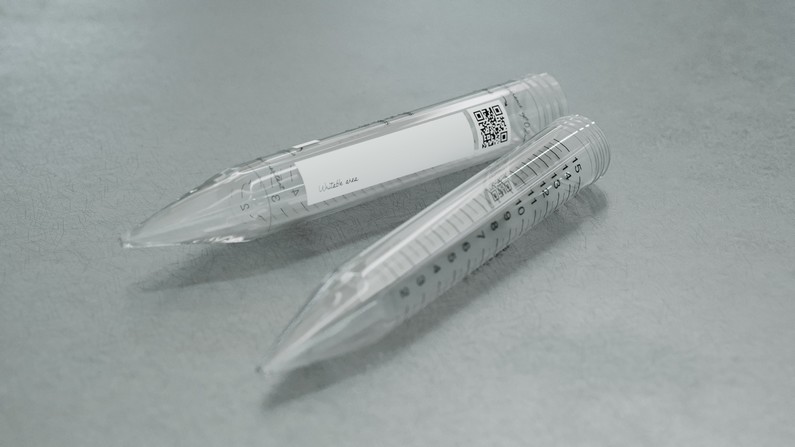
L'IML permet d'intégrer des graduations, un QR code ou encore une partie thermo-sensible (crédit photo : Kebo).
Résistante aux rayures, l’étiquette intégrée dans le moule des tubes sert à les doter d’une graduation pour indiquer le niveau de remplissage exact. Ce genre d'utilisation de l'IML est également intéressante pour les stylos à insuline ou les gobelets gradués médicaux, par exemple.
Une autre fonction potentielle de l'IML est la surveillance des profils de température. Il est en effet possible d'intégrer un élément à base d'encre thermochromique (sensible à la température), afin de permettre la détection d'une rupture éventuelle de la chaîne du froid : dès que la température du tube rempli dépasse 7°C, par exemple, l’encre en question change de couleur de manière irréversible.
Enfin, l'IML permet d'ajouter des informations sur le recyclage et la gestion des stocks au moyen d’un QR code.