Côté recherche
Des substituts osseux produits à l’aide de moules solubles imprimés en 3D
Le procédé Powder Injection Moulding (PIM) permet de créér des structures complexes, denses ou poreuses, à base de métal et de céramique. Il est mis en œuvre au sein du CRITT Matériaux Innovation dans le cadre du projet PIMyBone, pour produire des substituts osseux en phosphate de calcium.
Les problématiques cliniques liées à la reconstruction osseuse nécessitent des solutions polyvalentes dans leurs propriétés et leurs formes géométriques pour s’adapter aux différents sites opératoires. C'est précisément l'objectif recherché par le projet PIMyBone, débuté en décembre 2021, qui étudie le déploiement de la technologie PIM pour la production de substituts osseux synthétiques à taille de pores et taux de porosité variés, et au design adaptable.
Une grande variété d'applications dans le secteur médical
Ce travail a été réalisé dans le cadre du projet PIMyBone financé par l'Agence Nationale de la Recherche, au sein d’un consortium multidisciplinaire comprenant le laboratoire BIOS de l’Université de Champagne-Ardenne, l’institut ICCF - Clermont Auvergne INP, l’URD ABI – AgroParisTech et le CRITT Matériaux Innovation.
A mi-chemin entre l’injection plastique et le frittage des poudres, le PIM permet la fabrication en série de pièces de géométrie complexe à partir de nombreuses nuances de matériaux, comme les biomatériaux implantables dont les propriétés de biocompatibilité sont préservées. Parmi ces matériaux, il est possible d’injecter avec cette technique des granulés à base de TA6V, CoCrMo, 316L, alumine, zircone et, comme ici dans le projet PIMyBone, de phosphate de calcium.
Les exemples de produits issus du PIM sont nombreux, notamment dans le secteur médical qui illustre bien cette variété d’applications avec les brackets dentaires, les chambres implantables, les instruments chirurgicaux, les branches de lunettes…
On notera qu'il est possible d'atteindre un niveau élevé de détail des pièces produites sans opération de parachèvement, ce qui fait du PIM une solution économique pour la production en série de pièces complexes de petite ou moyenne taille.
Des pièces poreuses issues de poudre de céramique ou de métal
Le principe du procédé PIM s’appuie sur une succession de quatre étapes (Figure 1) :
- la fabrication de la matière première (Feedstock) sous forme de pellets composés d’un liant polymère et d’une charge métallique (MIM : Metal Injection Moulding) ou céramique (CIM : Ceramic Injection Moulding),
- l’injection dans un moule de forme pour obtenir une pièce dite "verte",
- un déliantage consistant à éliminer le liant pour obtenir une pièce dite "brune",
- et un frittage à haute température pour consolider la pièce.
Le produit fini, qui a subi lors du frittage un retrait dimensionnel de l’ordre de 20 %, peut être entièrement dense ou poreux lorsque des matrices de charge ou space holders sont incorporées au mélange. La taille, la forme et le pourcentage de vide ajouté définira les caractéristiques des porosités. Celles-ci sont modulables jusqu’à des taux de 80 % de macroporosités ouvertes et interconnectées de plusieurs centaines de microns de diamètre.
A cela s’ajoutent les microporosités de 1 à 10 µm qui dépendent, quant à elles, des conditions dans lesquelles est réalisée l’étape de frittage (température, durée) et qui détermineront le niveau de densification.
Ce double contrôle de la porosité confère en particulier aux biomatériaux, des caractéristiques morphologiques optimisées pour l’ancrage cellulaire, la réhabilitation osseuse et l’angiogenèse. Il est même possible d'obtenir une triple échelle de porosité, lorsque les macroporosités sont interconnectées.
L’un des verrous qui freine le déploiement de cette technologie est le coût d’investissement dans un moule de forme, d’autant plus onéreux que la pièce est complexe. C'est pourquoi un insert imprimé en 3D par dépôt de fil fondu (FDM) est utilisé pour les prototypages, préséries ou pièces sur mesure. Cet insert est constitué d'un matériau soluble dans l’eau qui s’élimine avec le liant et les matrices de charge en une seule étape.
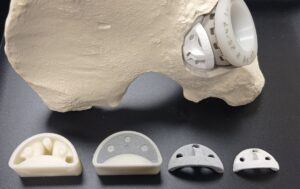
Figure 2a - Pièces de démonstration inspirées du système de révision acétabulaire Trabecular Metal de Zimmer (crédit photo : Critt Matériaux Innovation).
Deux pièces de démonstration
Pour démontrer le degré de personnalisation et de modularité qu'il est possible d'atteindre au niveau de la conception, deux pièces de démonstration ont été produites :
- la première inspirée du système de révision acétabulaire Trabecular Metal de Zimmer (Figure 2a),
- la seconde sur la base de blocs emboitables pour le comblement de grands déficits osseux (Figure 2b).
Ces deux produits présentent des caractéristiques dimensionnelles difficiles à obtenir par d’autres techniques de fabrication. Constitué de macroporosités autour de 250 µm de diamètre en moyenne et de microporosités avec un taux global de 75 % de porosités ouvertes et interconnectées, le biomatériau obtenu se comporte comme un scaffold (échafaudage) optimisé pour la recolonisation osseuse.
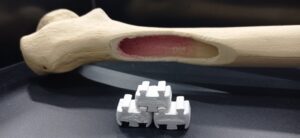
Figure 2b - Blocs emboitables pour le comblement de grands déficits osseux (crédit photo : Critt Matériaux Innovation).
Le mélange biphasé d’hydroxyapatite et de phosphate tricalcique β permet une résorbabilité adaptée selon le taux de β-TCP incorporé au mélange. Les températures de frittage sélectionnées assurent l’intégrité chimique des phases en présence tout en préservant les propriétés mécaniques.
Le projet vise également à synthétiser des phosphates de calcium dopés avec des ions zinc pour leur potentiel de régulation de l’inflammation, des ions cuivre pour limiter les risques d’infection ou encore des ions strontium pour promouvoir la repousse osseuse.
Les essais biologiques à venir permettront la validation finale du biomatériau.